Aldec
Alfa Laval Aldec centrifuges are designed for the sludge thickening and dewatering process in municipal and industrial wastewater treatment plants, as well as potable water works, solid waste plants, and biogas plants. Our decanter centrifuges focus on cost-efficiency, reliability, easy operation, and sustainability.
Experience the benefits of Aldec for sludge thickening and dewatering
- Reduces sludge volume during the sludge thickening and dewatering process, which cuts down on transport and disposal costs
- High capacity at small footprint: Compact, modular design saves space
- High performance combined with low energy consumption
- Wear-resistant design with anti-blocking feature.
- Complete, fully enclosed cleaning-in-place (CIP)
The extensive range of Aldec decanter centrifuges for sludge thickening and dewatering is capable of handling a wide range of flow rates. Designed to efficiently treat sludge in wastewater, they are simple to install, easy to maintain, and straightforward to operate. With minimal installation, operating, and service life costs, Aldec centrifuges provide a reliable solution for sludge thickening.
Sludge thickening and dewatering - Less water, lower cost
Cost-effective sludge thickening centrifuges are crucial for removing the water content from sludge in wastewater, as well as from industrial waste streams. The drier the sludge, the less space it takes up and the less it weighs – both resulting in big savings on transport and disposal costs, while helping to meet environmental requirements.
Low energy consumption and labour costs
When using Aldec decanter centrifuges in your sludge thickening and dewatering process, you benefit from low energy consumption and minimal maintenance costs, keeping dewatering expenses to a minimum. These centrifuges are also fully automatic, reducing labour costs while ensuring efficient processing of sludge in wastewater.
The features that make the difference
With more than 60 years of experience in solid-liquid separation, Alfa Laval knows everything needed to meet your challenges in sludge thickening and dewatering. Packed with features unique to Alfa Laval, Aldec centrifuges deliver reliable and high-performance solutions for treating sludge in wastewater.
FlightGuard
Robust wear protection for conveyor flights
FlightGuard wear protection consists of tiles welded to the conveyor of your decanter centrifuge, providing robust wear resistance and prolonged uptime in highly abrasive applications.
SolidsProtect
Flow-optimized solids outlet with wear protection
The innovative 360° outlet design ensures an even discharge of solids and minimal resistance. The outlet can handle high flow rates without blockages. SolidsProtect outlets feature replaceable wear saddles that maximize reliability and uptime of your decanter centrifuge.
FeedProtect
Feed zone with replaceable wear protection
The uniquely designed FeedProtect feed zone ensures gentle product acceleration and minimal turbulence, resulting in low abrasion and power consumption. The FeedProtect design is equipped with replaceable wear-protection liners, ensuring high uptime of your decanter centrifuge.
EasyLift
Spring loaded cover, that simplifies servicing
The patented spring-loaded hinged design makes it easy to open even the heaviest cover by hand. This also helps ensure quick, safe access for maintenance and service of your decanter centrifuge.
DeepPond
High separation performance and energy efficiency
Increasing the pond depth inside the bowl creates a larger volume, leading to longer retention time and improved separation performance. The DeepPond design delivers high solids dryness and clean centrate from your decanter centrifuge, even at high flow rates.
How do two-phase decanters work?
Learn how to improve efficiency in sludge thickening and dewatering
Separation of sludge in wastewater occurs in a horizontal cylindrical bowl with a slimline screw conveyor. The feed enters through a stationary inlet tube and is smoothly accelerated by an inlet distributor in the feed zone. Centrifugal force causes solids to sediment on the bowl wall. The conveyor, rotating slightly slower than the bowl, moves solids to the conical end. The cake exits through discharge openings into the casing. Separation takes place along the entire cylindrical bowl, and the clarified liquid exits through adjustable outlet tubes.
Sludge thickening and dewatering case stories
Related products for sludge thickening and dewatering
Contact us anywhere, anytime
At Alfa Laval, we recognise the importance of efficient sludge thickening and dewatering in maintaining reliable operations. With innovative solutions, expert support and a dedicated Global Service Network, we’re here to help you maximise uptime, optimise performance and achieve a stronger return on investment.
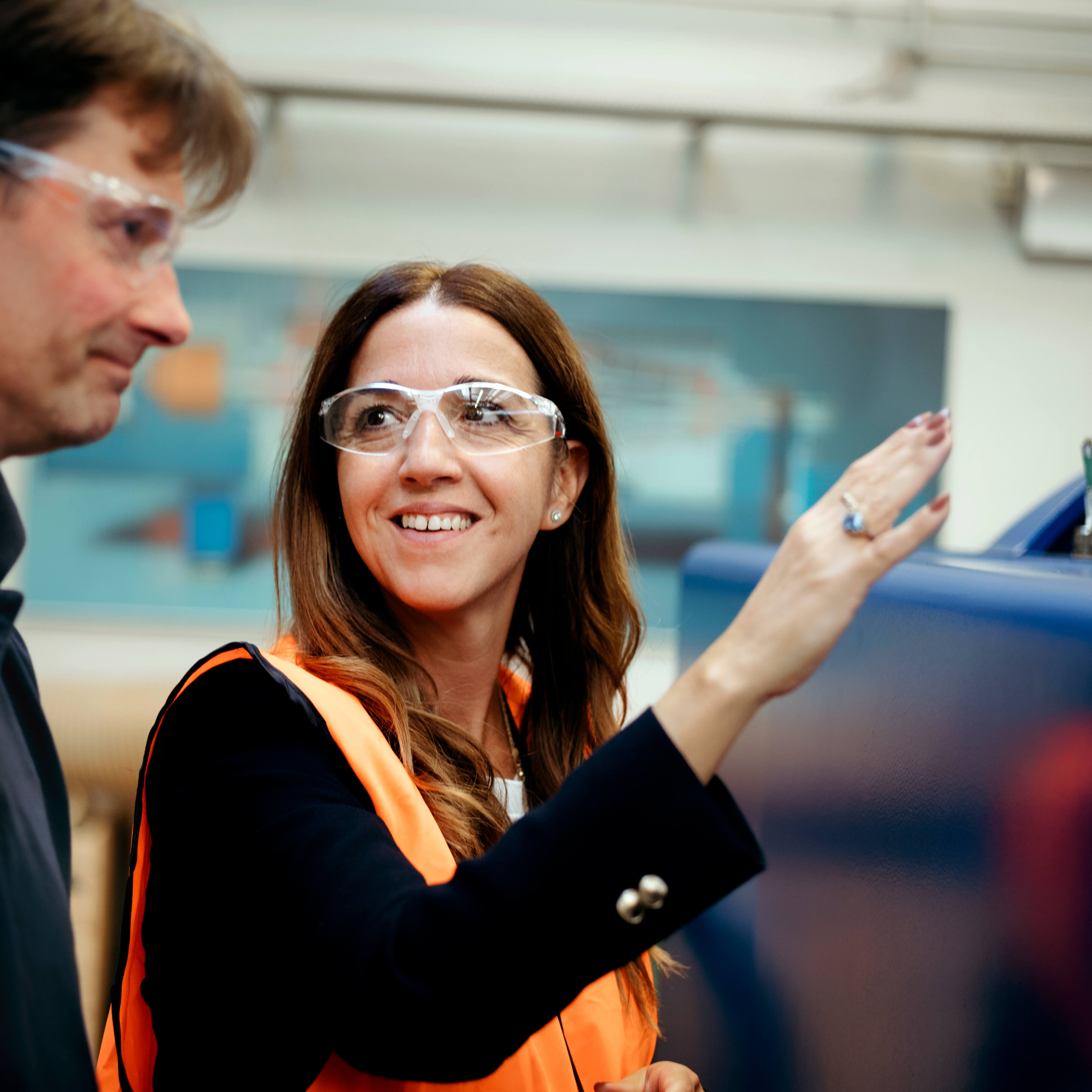