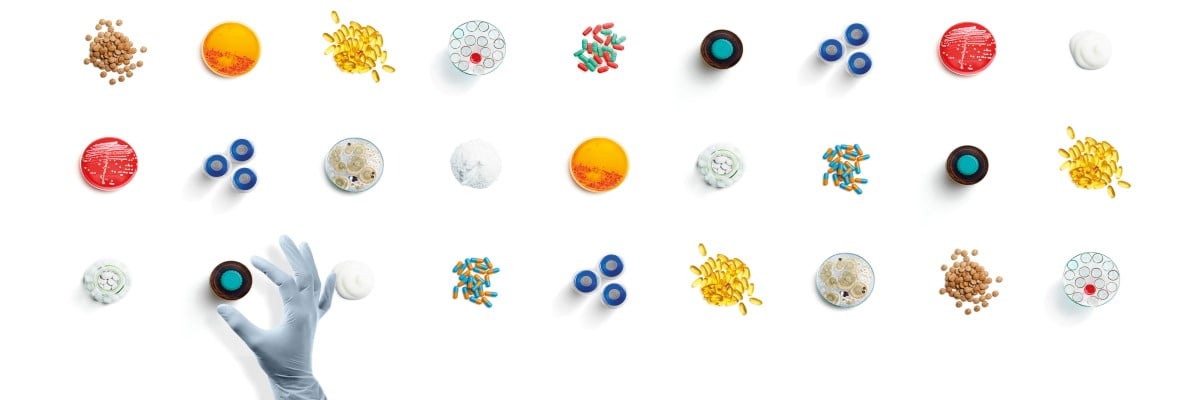
Preventing cross-contamination in pharmaceutical water distribution loops
Cross-contamination occurs whenever any foreign substance is introduced into the water. The source of contamination may stem from equipment in the form of wear particles, residues left on the equipment during manufacturing, or substances from operations such as gear box oil, lubrications, and cooling or heating media. Equipment together with the correct installation of the equipment in the system helps ensure that the water system is a closed-loop system without any risk of contamination from the environment outside the system. Choosing the right equipment helps reduce the risk of cross-contamination in pharmaceutical water distribution loops. Below are a few things to keep in mind to make sure that you select the right equipment and thereby minimize the risk of cross-contamination in your system.
System design and equipment selection help optimize pharmaceutical manufacturing
Having supplied equipment to the global biotech and pharmaceutical industry for decades, we at Alfa Laval have seen the challenges that the industry is facing. When looking at pharmaceutical water systems and specifically at the distribution loops, we see the biggest challenges nowadays are coming from bacteria and biofilm, rouging and cross-contamination. To help our customers solve these challenges while at the same time optimizing the total cost of ownership, we will share our experience in a series of articles.
In this article, we will take a closer look at cross-contamination.
Preventing cross-contamination in pharmaceutical water distribution loops is one of the major challenges facing biotech and pharmaceutical companies today.
The most common cause of cross-contamination is selecting the wrong equipment. By selecting the right equipment, you will not only minimize the risk of cross-contamination, but also will reduce operating costs and downtime due to service and maintenance. Even the smallest design issue of a single component can impact the entire system.
The right equipment not only contributes to delivery of the specified quality and quantity of water, but also to the safety, efficacy and quality of highly purified water and, more importantly, of the final product.
Selecting the right equipment
To ensure reliable, consistent production in pharmaceutical water distribution loops, it is critical to select right equipment. Choosing pumps, valves, heat exchangers and tubes and fittings designed to minimize the risk of cross-contamination ensures that pharmaceutical manufacturers can maximize uptime and minimize downtime while protecting pharmaceutical product purity, safety, quality and integrity.
Click on each of the following options to learn more.
Centrifugal Pumps
The target:
Pumps are essential to transport water to the point of use at the right flow and to secure the circulation of water in the distribution loop. The circulation of the water is needed to maintain the desired temperature of the water throughout the entire system as well as to generate sufficient shear forces in the loop. This helps prevent entrapment of debris as well as helps minimize biofilm buildup on the surfaces.
The challenge:
All rotating equipment generates wear. Centrifugal pumps have a shaft seal where a rotating seal turns around an axis on a stationary seal. The small space in between the seal faces must be lubricated with water to minimize direct contact between the seal faces as well as to minimize the generation of wear particles from the two faces grinding against each other. As we all know, these shaft seals are worn down and need to be replaced at certain intervals.
Current Good Manufacturing Practice (cGMP) regulations state that product contact surfaces must not be reactive, additive or absorptive, which means that wear particles generated from the shaft seal must not be added to the distribution loop.
The solution:
Select a pump with an external shaft seal, which has its outer diameter facing the outside of the pump. The centrifugal forces from the rotating seal will force the water to move from the inside to the outside of the pump. This ensures the development of a lubricating film between the seal faces while minimizing seal wear and generation of wear particles from the seal. Furthermore, it is inevitable that some wear particles are generated from the seal faces; selecting an external seal shaft ensures that any wear particles generated will be transported out of the loop due to the centrifugal forces.
What’s more, pharmaceutical water – especially water for injection (WFI) – is very pure and free from other ions, except from H2O. This makes the pharmaceutical water “dry” and provides limited lubrication of the seal faces. The friction that is generated between the seal faces creates an electrical charge on the seal faces. If seal faces with different conductivities are used, an electrical arcing between the faces takes place, causing pits where SiC is oxidized to SiO2. These pits will further increase the wear between the seal faces and further minimize the lifetime of the shaft seal. This phenomenon is called electrochemical corrosion.
All Alfa Laval UltraPure centrifugal pumps have external shaft seals, which ensure the best possible lubrication of the seal and prevent wear particles from entering the closed-loop system. The Alfa Laval LKH UltraPure pump also has an enhanced SiC shaft seal with the same conductivity for both seal faces; this minimizes the risk of electrochemical corrosion, further minimizes the generation of wear particles and extends the lifetime of the shaft seal.
The Alfa Laval LKH UltraPure pump is also the most energy-efficient pump available today, thereby ensuring the lowest possible energy consumption and the lowest possible operating cost of your system.
Diaphragm valves
The target:
Diaphragm valves are the recommended valve (by ASME BPE) for pharmaceutical water systems. The diaphragm valve should provide a dynamic seal within the process as well as a seal between the process and the atmosphere. The diaphragm valve should also be able to close, open, divert or control the fluid in the system. Ensuring that the valve provides a seal both within the system and between the atmosphere and the water is crucial in order to prevent cross-contamination.
The challenge:
All components in the water system must be hygienically designed without any dead-legs, crevices or pockets. Diaphragm valves are particularly susceptible to wear and tear. Weir-type diaphragm valves with polytetrafluoroethylene (PTFE) diaphragms are commonly used in water systems. These typically consist of a PTFE face and an ethylene propylene diene monomer (EPDM) backing. This combination is intended to provide resiliency and compression during valve actuation. However, the PTFE face is prone to wear and tear and generally ruptures before the more durable EPDM backing.
Should a tear occur, a large crevice forms between the two materials, providing a breeding ground for microbes. The crevice not only traps bacteria, but also traps nutrition which makes this crevice or pocket to a suitable habitat for bacteria to grow and for biofilm to develop. This biofilm will later extend into and contaminate the water in your system. Worse yet, detecting a tear in the PTFE face is only possible when the valve is disassembled and manually inspected, after cross-contamination has taken place. This crevice will not only trap bacteria but also cleaning and passivating agents that are used after servicing and maintaining the water system. During the flushing of the system, it will be very difficult to remove these chemicals from the crevice and the system; these will then migrate out from the crevice and contaminate your water during normal operation.
The solution:
As an alternative to the PTFE/EPDM diaphragm, Alfa Laval offers a high-grade single-layer EPDM diaphragm, which meets the requirements of pharmaceutical water systems. This EPDM diaphragm has proven to be very inert in pharmaceutical grade water and does not leach any colour or chemicals to the water. Furthermore, it is developed for high-temperature conditions and can even stand continuous steaming. The Alfa Laval DV-ST UltraPure diaphragm valve has flat connection surfaces above and under the diaphragm; no steel ridge pinches the diaphragm, which means that no additional stress is put on the sensitive diaphragm material. The lack of steel ridge will extend the lifetime of the valve and will minimize the risk of diaphragm cracks, which generally occur when using two-layer PTFE/EPDM diaphragms instead of a single-layer EPDM diaphragm.
All Alfa Laval DV-ST UltraPure diaphragm valves are fitted with leak detection holes to facilitate detection of diaphragm breakage; this helps reduce the risk of contamination. What’s more, all forged and block valves feature valve bodies with low delta-ferrite content and specified sulphur content, which contribute to superior weld quality and minimize the risk of rouging in your system.
Compact, lightweight and versatile, this safe and crevice-free diaphragm valve has a modular design. This makes it easy to tailor the valve to the exact requirements of individual pharmaceutical water distribution loops. It delivers reliable, contaminant-free performance and ensures the safe, long-term operation of the system.
Shell-and-tube heat exchangers
The target:
Shell-and-tube heat exchangers are the most commonly used heat exchangers in pharmaceutical water distribution loops. Bacteria in water systems are typically controlled by heat. In hot water loops, the temperatures are kept high, generally between 55°C and 95°C to prevent bacterial growth. Cold water loops are typically sanitized by heating the water to above 60°C. The higher the temperature, the faster the bacteria will be killed and the system will be sanitized. After sanitization, the water is then chilled to the starting temperature. The faster the water is chilled, the less likely it is that bacteria will grow. This is particularly true when the temperature approaches the interval from 45°C to 35°C.
Heat exchangers are also used to cool water from hot water loops to a lower temperature. This is sometimes required when the water is to be mixed with heat-sensitive medicines, or if it will be used to wash utensils manually in order to prevent scalding the hands of the person washing the utensils. It is also important that the cooling occurs quickly to prevent bacterial growth.
The challenge:
Cross-contamination risks are inherent in the design of shell-and-tube heat exchangers. The heat exchanger uses a cooling or heating media to transfer heat either from or to the pharmaceutical grade water. This water does not have the same quality as the water in the loop. If there is leakage in the heat exchanger, there is a risk that the pharmaceutical grade water will be contaminated. To avoid cross-contamination from the cooling or heating media, double tube sheet shell-and-tube heat exchangers are used; the welding of the inner tubes is made on the outer tube sheet. This design eliminates the risk of cross-contamination because, if a weld fails, there is no leakage out of the system and no contact with the cooling or heating media. A leakage in the weld is also easily detected by the operator since the weld is visible from the outside. Another critical design component is the expansion of the inner tube to the inner tube sheet. If this connection is not 100% tight, there will be a crevice between the inner tubes and the inner sheet. If this occurs, there is a significant risk of crevice corrosion between the two surfaces. This crevice corrosion will later lead to a breakage of the inner tubes, which means that the cooling or heating media will contaminate the pharmaceutical grade water. Unfortunately, crevice corrosion and leakage are seldom visible and therefore very difficult to detect in advance.
The solution:
To meet the demands of pharmaceutical water distribution loops, selecting shell-and-tube heat exchangers designed for hygienic applications and with high-quality welding and tube expansion is highly recommended. With the Alfa Laval Pharma-line shell-and-tube heat exchanger, we have paid extra attention to high-quality welding and high-quality expansion of the inner tubes. Every welder is thoroughly trained and qualified. Every weld is executed according to established standard operating procedures, and every weld is logged and controlled according to the highest quality assurance practices. We also devote extra attention to the expansion of the inner tubes in order to ensure that there is no risk of crevice formation and crevice corrosion. We also use an extra large bending radius to provide the best possible surface finish in the bending areas; this minimizes the risk of biofilm growth. The Alfa Laval Pharma-line offers high-quality welds and tube expansion, crevice-free design and seamless tubes with smooth surface finishes to minimize the risk of cross-contamination and biofilm growth. All components undergo rigorously controlled manufacturing techniques, including welding, tube expansion, tube bending and polishing.
Tubes and fittings
The target:
Tubes and fittings should only connect the various components and user points in the loop. By doing so, they must ensure that this connection is encapsulating the water from the environment and has negligible impact on the system. During installation of the water loop, tubes and fittings should facilitate easy welding, cleaning, passivation, rinsing, and draining of the loop.
The challenge:
In a typical water distribution loop, tubes and fittings take up a surface area of more than 90% of the total system, comprising by far the largest portion of the product contact surface area. Tubes and fittings therefore pose the biggest risk of material contamination to the water system. The cGMP (US FDA 21CFR211.65 a) states: “Equipment shall be constructed so that surfaces that contact components, in-process materials, or drug products shall not be reactive, additive, or absorptive so as to alter the safety, identity, strength, quality, or purity of the drug product beyond the official or other established requirements.”
Polishing residues on the surface of tubes and fittings are difficult to remove during cleaning and passivation since they are pressed deeply on and into the surface. These polishing residues will later migrate into your water while operating your water loop. The polishing residues will also generate rouge particles in your system that will further contaminate your water.
During construction or installation of a water loop, the cost of installing the tubes and fittings is typically more expensive than the tubes and fittings. Material quality and wall thickness in the weld ends are of paramount importance to secure good welding. If the welding quality is insufficient, the weld must be cut out and a new piece must be welded in its place with two welds. High-quality tubes and fittings will minimize the need for rewelds. Poorly polished surfaces with polishing residues pressed into the surfaces are difficult to clean. If the surfaces are not thoroughly cleaned, the surfaces cannot be passivated. High-quality polishing, ensuring that the surfaces are free from polishing residues, will facilitate quick, easy cleaning and passivation.
The solution:
Choosing tubes and fittings that are inert (not reactive, additive, or absorptive) will help minimize the risk of material contamination. Alfa Laval Tri-Clover® UltraPure tubes and fittings are polished and cleaned using proven standard operating procedures that have served the pharmaceutical industry for decades. Alfa Laval only works with proven preferred suppliers of raw materials that are optimized for welding. In the Alfa Laval factory, we conduct thorough quality control of all fittings. For each and every fitting, we ensure chemical conformity, surface roughness and appearance, exact dimensions (including wall thickness, ovality, square ends, etc.), marking, packaging and labelling. Alfa Laval tubes and fittings also meet the requirements of ASME Bioprocessing Equipment (BPE) Certification.
Alfa Laval Q-doc: Well documented to safeguard quality
To reduce contamination risks, downtime and costs, all Alfa Laval UltraPure equipment and components for the pharmaceutical industry are backed by Alfa Laval Q-doc. Based on Good Documentation Practice (GDP), Q-doc is a comprehensive documentation package for Alfa Laval UltraPure pumps, valves, heat exchangers, and tube and fittings. It provides full transparency of the entire equipment and replacement parts supply chain – from raw material to final delivery.
Alfa Laval Q-doc comprises a conformity declaration, material certificates, relevant test certificates and information about necessary Alfa Laval spare parts kits for standard components. With Q-doc, customers receive transparent and well-documented quality assurance of the sourced equipment. It traces every change in material or manufacturing procedures, including details about product contact parts such as steel and gaskets. This assures product safety as well as facilitates purchasing, installation, qualification, validation and change control procedures. In a word, Q-doc safeguards pharmaceutical water distribution loops against cross-contamination, providing long-term peace of mind.