Upgrading brewery deaeration system improves craft beer
Process optimization goes hand in hand with sustainability at Vocation Brewery, one of the UK’s largest independent craft breweries. When adding a deaeration system, the brewery wanted to enhance product quality and efficiency while reducing the environmental impact of its operations. Alfa Laval Aldox™ Mini deaeration module helps boost productivity and product quality by producing high-quality deaerated and carbonated water and raw liquor for the brewing process.
DATE 2024-03-12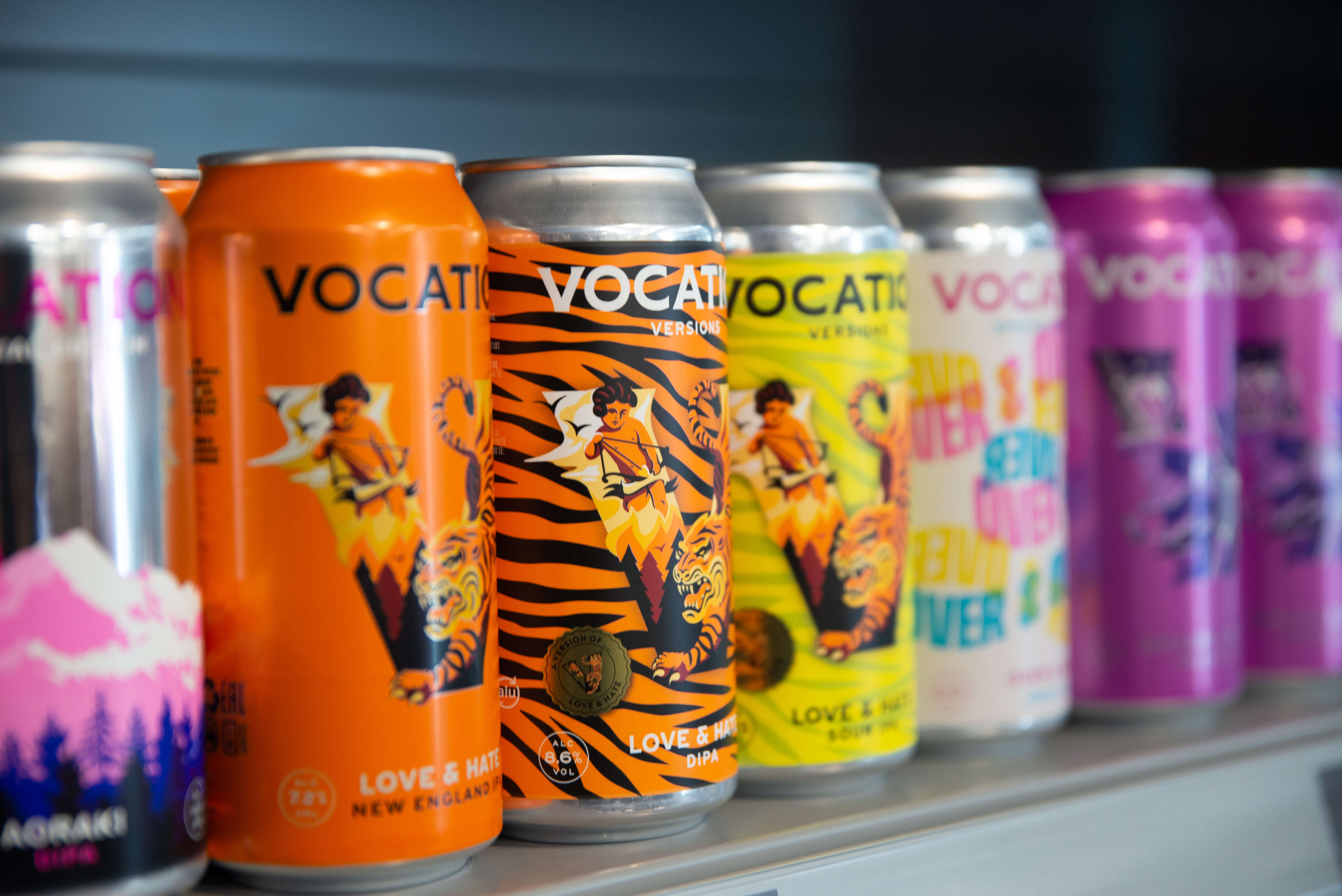
From its humble beginnings in 2015, Vocation Brewery has become one of the UK’s largest independent craft breweries. Two years later, the brewer invested in an Alfa Laval Brew 80 disc stack separator to use after the fermentation process. Today, the company produces over 10 million pints of stout, pale ale, IPA and lager a year for distribution to 40 countries worldwide.
“Integrating the separator into our process was incredibly straightforward due to close collaboration with the Alfa Laval engineering team,” says Matt Howgate, Director of Brewing at Vocation Brewery.
Increased capacity, higher yields, uncompromising quality
To determine whether adding an onsite deaeration plant was the right choice for the craft brewery, Matt toured a few other breweries. The brewer chose the Alfa Laval Aldox™ Mini for its high separation efficiency, compact footprint, large surface area to separate gases from the liquids, ease of use and advance control system.
“Seeing an onsite deaeration system at work showed us how having our own deaeration plant at Vocation Brewery could take our business to the next level, increasing production capacity and overall yield from each brew without compromising on quality,” explained Matt. “It’s unusual for a brewer our size to install a deaeration system onsite. It’s mostly the large international breweries that decide deaeration is a must.”
After fermentation, it is imperative to deoxygenate any water or raw liquor that comes into contact with the beer since any dissolved oxygen can have adverse effects on the taste and stability. Initially, Vocation Brewery purchased and installed the Aldox Mini to finetune its craft beer to ensure better tasting beer before packaging the product.
“We saw the Aldox Mini achieved more efficient oxygen removal at low flow rates and a higher quality of deaerated water and raw liquor,” Matt continued.
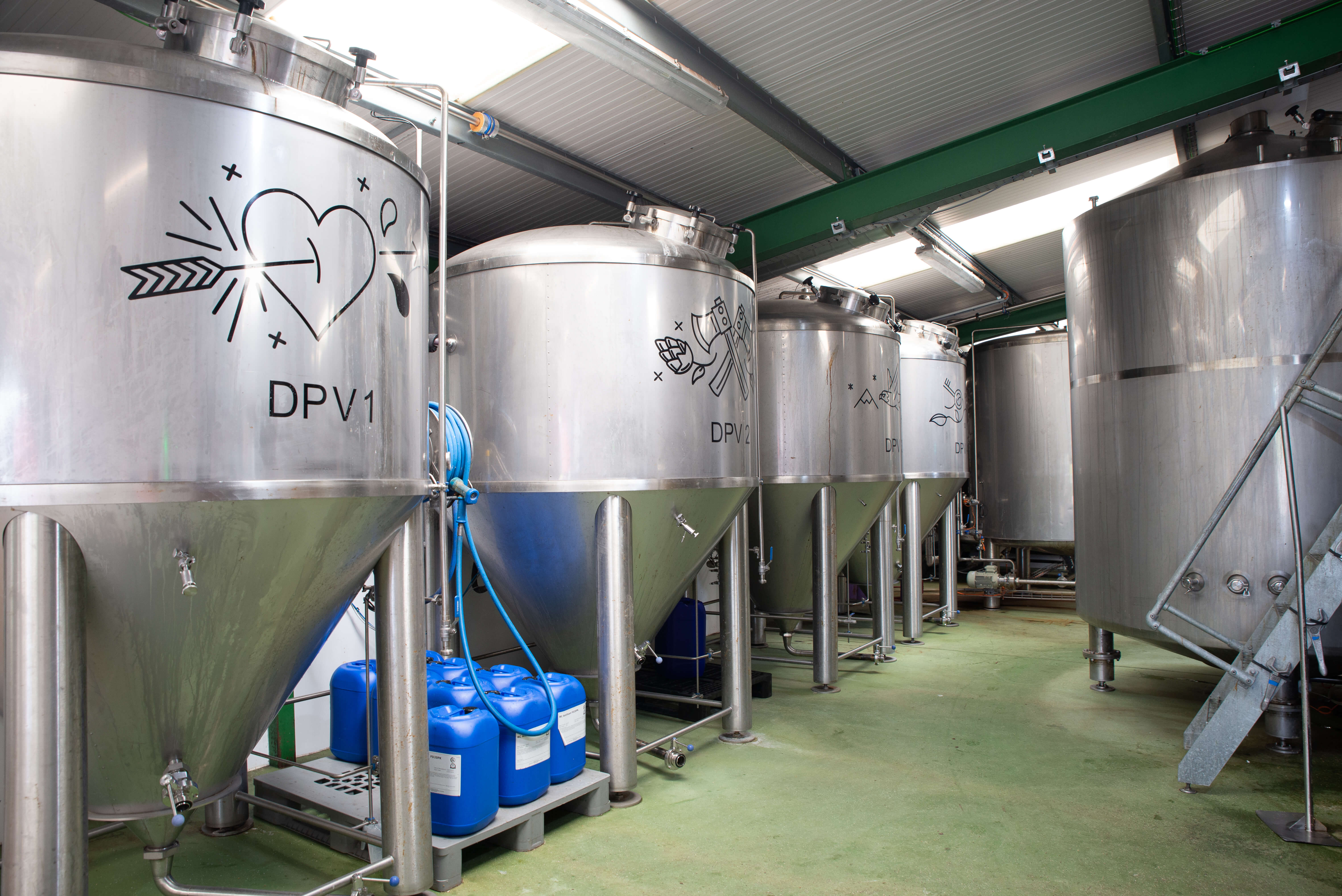
Better quality control and more sustainable pipeling purging
The brewery has since expanded its use to dilute high alcohol beer to its normal strength, using deoxygenated water to correct fluctuations in the alcohol-by-volume measurements. Deaeration helped improve quality control of Vocation Brewery’s product portfolio.
Vocation began to flush its lines with deaerated water rather than carbon dioxide, reducing the dissolved oxygen content in water and raw liquor and safeguarding the beer. Doing away with the conventional use of boiled water and carbon dioxide to purge piping systems makes the process more sustainable.
The separator and staff were top-notch, so when we were looking to invest in a new deaeration processing line five years later, I had only one company in mind.
Matt Howgate, Director of Brewing at Vocation Brewery
Higher productivity with rapid deoxygenation
Before installing the Aldox Mini, the brewery used a stripping gas (CO2) to produce deaerated water, which required more time and left more dissolved oxygen in the water. In less than five minutes, the Aldox Mini reduces the dissolved oxygen in the water below 10 ppb, enabling the brewery to produce higher quality beer in less time.
“We’ve significantly ramped up our onsite production of deaerated water,” notes Matt with a grin. “Producing up to 30 hecto litres of deaerated water per hour is a huge step up from what we used to produce. That more than meets our requirements now and leaves room to expand in the future.”