AGC aims for sustainable caustic soda concentration system through process optimization
AGC, one of the world’s largest glass manufacturers, has gone through a technology conversion from shell and tubes to gasketed plate heat exchangers, including use of HeatSealTM gaskets, at its Chiba Plant in Japan, to improve the efficiency of manufacturing processes and to reduce environmental impact.
DATE 2023-11-28AGC has replaced a one evaporator and four heat exchangers (economizers) in the caustic soda concentration process at its Chiba Plant with Alfa Laval plate heat exchangers and a specially designed evaporator. The result is a 10% reduction in steam consumption. Additionally, downsizing the pumps has resulted in a lowered electricity consumption and reduced equipment space required. Also, with the reduced frequency of gasket replacement due to improved quality, the time and cost of maintenance will be reduced.
The challenge of chemical manufacturing toward decarbonization
New energy and material solutions attract attention in the efforts to work toward the realization of a decarbonized society. However, a major challenge for chemicals, which play a fundamental role in many industries, is how to improve the efficiency of manufacturing processes to reduce environmental impact.
AGC has developed its chemicals business domain from the manufacturing of soda ash, one of the raw materials for glass. The manufacturing process for caustic soda, one of its main products, has been adapted to meet current needs for improved quality, reduced environmental impact, and cost reduction.
We believe it is important for us to provide a stable supply of caustic soda to the world by building a more sustainable and safer manufacturing process under AGC Chemicals’ vision; Creating a safe, secure, comfortable and environmentally friendly world with chemical technology. To this end, it is important to increase the plant’s operating rate and minimize problems.
- Shunsuke Okada, lead process designer at AGC
Yuu Kang explains that “The caustic soda concentration process had three major challenges. First, the aging shell-and-tube evaporators were costly to maintain. Second, the caustic soda electrolysis plant consumed a large amount of energy, so we had to review the process design to reduce energy consumption to meet our sustainability goals. Third, the gaskets of the existing plate heat exchangers installed in the concentration process had to be replaced more frequently than scheduled due to the risk of leakage.”
Because the concentration process involves the handling of dangerous materials, a leak could lead to a major accident, which would further prolong plant shutdown. Caustic soda is one of the main products produced in the plant, and the other main product is chlorine gas which is used for other processes inside the plant, so a shutdown would have far-reaching consequences.
Energy efficiency through process improvement
As the solution to the problems listed, AGC choose Alfa Laval’s gasketed plate heat exchanger and the newly developed HeatSealTM gasket. The gaskets use Aflas 600X, a fluoroelastomer developed by AGC, which has significantly improved heat resistance and oxidation resistance compared to conventional gaskets, and can be used for continuous operation at temperatures up to 210°C. “This material has properties like an intermediate between resin and rubber, and is characterized by its resistance to strong acids, alkalis, and heat. Thus, it can be used in gasketed plate heat exchangers where amine resistance is required, which is a major advantage over conventional fluoroelastomers. It is used for semiconductors, electric cables, and offshore for special parts used in resource drilling,” said Mr. Kawai of the Chemicals Development Department.
AGC’s sister plants outside of Japan already have experience with Alfa Laval’s plate heat exchangers using HeatSealTM gaskets. Takuya Yoshikawa, responsible for the equipment at AGC, says, “When we introduced the gasket, we were of course expecting improved gasket durability, smaller equipment, and easier installation and maintenance. We were able to reduce the size of the pump by more than 5% compared to the conventional pump, and the reduction in the electricity cost for the pump alone has had a great effect. In addition, Alfa Laval’s evaporation and concentration process specialist Tomas Kovacs was able to help us from the beginning with knowledge we didn’t have, on how to rethink the process to make it more energy efficient. We are very pleased with the results.”
Further possibilities
“In our efforts to save energy in the electrolysis process, we were able to reduce energy cost by hundreds of thousands of euros. Information on this initiative is being shared with our other facilities around the world who I believe will consider to introduce this technology. At the Chiba plant, we are planning to replace the rest of the existing shell-and-tube heat exchangers with Alfa Laval’s plate heat exchangers to increase efficiency, save space, and reduce maintenance costs.” says Mr Yuu Kang, Manager, Production Department who is also looking forward to future developments. “In addition to energy efficiency, we expect to reduce maintenance costs significantly. We are looking forward to Alfa Laval’s efficient service to complete the inspection and replacement on a tight schedule.”
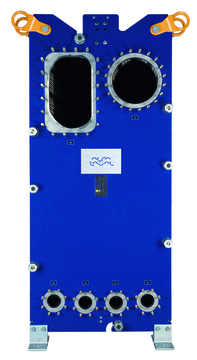
Models
- 1 x AlfaVap 650 (nickel)
- 2 x TL10P (nickel with HeatSealTM gaskets)
- 2 x TL10B (nickel with HeatSealTM gaskets)
Energy savings
10% reduction in steam consumption as well as electricity consumption reductions.
Uptime
Lesser frequency of gasket replacement reducing downtime and maintenance costs.
Technology shift
From shell-and-tubes to gasketed plate heat exchangers with HeatsealTM .