A wastewater plant's creative upgrade
For more than 20 years, the Gwinnett County F. Wayne Hill Water Resources Center, relied on six Alfa Laval Sharples DS-706 decanter centrifuges to process and dewater wastewater biosolids. While these machines had performed reliable, the team recognized that advancements in technology could offer greater efficiency and sustainability. Eager to explore more eco-friendly solutions, they set out to upgrade their equipment, aiming to reduce waste and operational costs while embracing a more sustainable future for the facility.
DATE 2025-01-23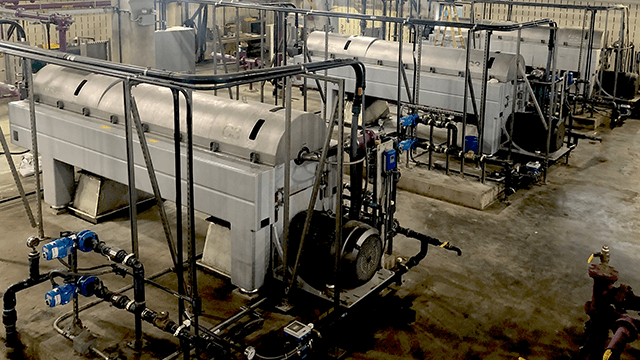
The challenge
The Gwinnett team faced a significant challenge – their environmental footprint while managing the immense cost of sending countless tons of dewatered biosolids to landfills each year at the cost of over $6 million. The team needed to find an innovative way to turn these biosolids, the byproduct of their wastewater facility, into something valuable. How could they transform what was once considered waste into a marketable product, like fertilizer, that offsets costs and contributes to sustainability?
The solution
Understanding the project’s magnitude, the Gwinnett team approached it with a long-term, phased strategy. The first critical step was to upgrade their infrastructure- They collaborated with Alfa Laval’s water team and opted to modernize their control panels, integrating advanced logic, real-time monitoring, and superior decanter control capabilities. These upgrades provided greater operational control and improved efficiency, increasing the dryness of the biosolids while significantly reducing energy consumption and polymer usage.
One of the most transformative steps was replacing their 20-year-old decanters with Aldec G3 125 decanters. These advanced decanters deliver higher performance and efficiency, all while using fewer resources. The team already saw significant improvements with their installation, but the vision continued.
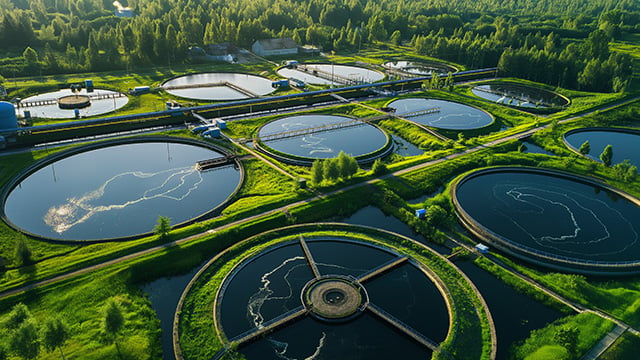
Next steps
Looking ahead, the next phase of the project promises to be even more impactful. The team plans to install dryers capable of removing 90% of the remaining water content from their biosolids. Once dried, the resulting product can be sold as high-quality fertilizer, turning what was once a costly waste product into a profitable resource. In addition to generating revenue, these dryers will eliminate the need for costly landfill hauling, further slashing operational expenses.
The ALDEC G3 decanters will continue to contribute in this phase, as their ability to extract more water than their predecessors mean the dryer will require less energy to complete the job, further optimizing the process and increasing the project’s cost-efficiency.
A vision for the future
Gwinnett County is embarking on an exciting journey towards a more sustainable future. Their dedication to reducing environmental and financial impact of their wastewater facility is a testament to their forward-thinking leadership. By transforming waste into valuable fertilizer, they’re not only cutting costs for their taxpayers but also contributing to a circular economy. This project showcases how modern wastewater treatment plants can integrate innovative solutions to achieve both environmental sustainability and operational efficiency.
The Gwinnett team’s commitment to inversing in cutting-edge technology and thinking outside the box has set a powerful example for other municipalities to follow. Their partnership with the team at Alfa Laval reflects a shared mission to build a cleaner, greener future – one that benefits both the local community and the environment at large.
The journey continues, and with Gwinnett County is paving the way towards a sustainable tomorrow. Alfa Laval is proud to support them every step of the way, as together, we prove that innovation and sustainability go hand in hand.
Results
Aspect improved |
Before (DS-706) |
After (G3-125) |
Impact |
Cake dryness |
21% |
23% |
Close to 6000 tons less to truck to landfill - saving hundreds of thousands of dollars a year |
Solids recovery |
~96% |
~99% |
Greatly reducing the need to reprocess large amounts of solids through the system |
Polymer usage |
15-17% less |
~$300,000 less in annual polymer costs |
|
Energy usage |
~45 to 50% reduction |
Varies with energy cost and loading but, for 6 large machines, the difference can be hundreds of thousands of dollars a year |