Alfa Laval enhances municipal wastewater operations in Colombia through Remote Support and Monitoring
Alfa Laval's remote support and monitoring solution has transformed a municipal wastewater customer’s operation in Colombia, optimizing production and reducing costs. Municipal wastewater treatment plants play an essential role in maintaining the cleanliness and environmental sustainability of cities. However, like any complex system, these plants often face challenges that can impact their efficiency and productivity.
DATE 2025-02-24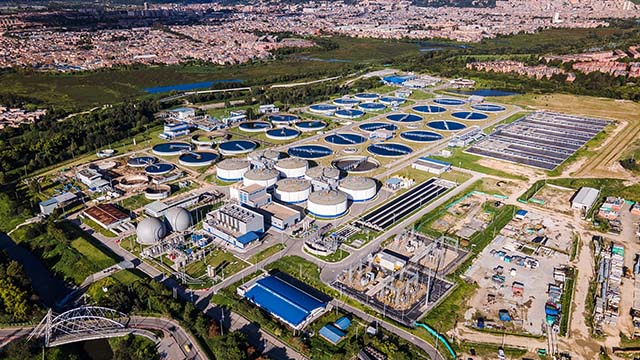
Alarmed by the potential operational consequences, a municipal wastewater plant in Colombia sought a solution that could ensure the continuous operation of their wastewater treatment processes while minimizing the need for on-site intervention. That's when they turned to Alfa Laval’s Remote Support and Monitoring for a decanter centrifuge. This solution not only addressed their existing challenges but also provided numerous additional benefits.
Alarms had been triggered on the decanter in operation at the plant. To overcome the alarm-triggering issue, Alfa Laval's technical experts leveraged their expertise using the Alfa Laval portal, analyzed the alarm data, and promptly notified the customer and their sales representative about the situation.
Through this analysis, the root cause of the alarms was identified: a low CPU battery level. This seemingly small issue had the potential to lead to parameters deletion, requiring an on-site field service engineer to reload them. By detecting this issue early on, Alfa Laval's experts were able to recommend replacing the battery promptly, preventing any further complications and disruptions to production.
Harnessing the capabilities of Alfa Laval's Remote Support and Monitoring solution brought a multitude of benefits to the municipal wastewater customer:
- Proactive Contact: The customer enjoyed the peace of mind that came from proactive communication with Alfa Laval's technical expert. Instead of being caught off guard by potential issues, the customer was notified in advance, allowing them to take proactive measures to maintain operational efficiency.
- Time and Cost Savings: With Alfa Laval's Remote Support and Monitoring services, the need for an on-site field service engineer visit was eliminated, which may amount to close to 700 EUR in the case of such event. This not only saved the customer valuable time but also reduced costs associated with unnecessary travel and on-site support. Troubleshooting and resolution were achieved swiftly and effectively through remote guidance, minimizing downtime.
- Continuous Production and Efficiency: By promptly replacing the low CPU battery, the customer ensured uninterrupted production and eliminated the risk of product losses or wasted raw materials. This continuous operation and improved efficiency contributed to the overall success of the wastewater treatment process.
In addition to enhancing operational efficiency and productivity, Alfa Laval's Remote Support and Monitoring solution also assisted the customer in their journey towards environmental sustainability. Through the optimized production and reduced intervention from on-site personnel, the customer saved approximately 8 kg of CO2 emissions.
By combining technical expertise with proactive monitoring, Alfa Laval empowered the customer to overcome challenges, optimize production, and enhance their overall operations. As more organizations seek innovative solutions to drive efficiency and sustainability, Alfa Laval stands ready to deliver effective and tailored solutions to meet their needs.
Highlighted technologies
Cost savings