Sicit unleashes the power of Alfa Laval ConditionAlert™
At Sicit, an innovative company in Vicenza, Italy that converts processing residues from leather tanning into protein hydrolysates, the operations rely heavily on the performance of their decanters. Recognizing the importance of moving to preventative and predictive maintenance, and keen to secure uninterrupted operations, Sicit turned to Alfa Laval's ConditionAlert™ solution to monitor their decanters and ensure optimum performance.
DATE 2025-02-24Since implementing ConditionAlert™ in 2022, Sicit has experienced the power of this advanced condition monitoring system. However, it was in March 2023 that ConditionAlert™ truly proved its worth. ConditionAlert™, a core component of Connected Services, identified damage developing on the main bearing of one of the decanters. Within moments, an Alfa Laval technical expert at its Adriatic Service Centre was alerted and swiftly contacted the customer.
To avoid any potential major failure, the decision was made to replace the faulty rotating assembly with a spare from Sicit's on-site inventory, while the damaged component was sent to the Service Centre for inspection. This quick response and action were made possible by the real-time intelligence provided by ConditionAlert™.
Early detection and swift action
In the weeks that followed, ConditionAlert™ continued to monitor the new rotating assembly and detected anomalies in the bearing. Recognizing the potential for future damage, an Alfa Laval technical expert instructed Sicit to perform lubrication as an initial remedy. But as additional vibration trends emerged, it became clear that the new assembly also had bearing damage.
With the vibration levels escalating, Alfa Laval recommended that the customer swap the new rotating assembly with the repaired one. Thanks to their quick response and seamless communication, a critical breakdown was averted, saving Sicit from extended downtime and hefty service costs, and preventing the negative environmental impacts that would have resulted.
The positive impact of ConditionAlert™ has been profound for Sicit. The ability to identify potential failures before they occur has become a crucial aspect of their equipment's reliability. It's no secret that customers like Sicit demand uninterrupted operations and minimal disruptions. ConditionAlert™ is precisely the solution they needed to achieve this goal.
The future of customer support through predictive maintenance and IoT solutions
Alfa Laval Adriatic team acknowledges the significant impact of ConditionAlert™: "In Sicit, we have had several cases in which ConditionAlert™ findings and recommendations saved the customer from an unplanned breakdown. Any alternative would have caused the customer a massive cost impact."
Looking towards the future, Alfa Laval is determined to make Connected Services an integral part of its offering. By combining separation know-how with the power of Internet-of-things-enabled solutions like ConditionAlert™, Alfa Laval is setting a new standard for customer experience and support. Their growing network of local experts and digital solution centres ensures that customers receive top-notch service backed by unparalleled data-driven insights.
Andrea Pelizzaro, Connected Services Manager at Alfa Laval, envisions a brighter future for their customers: "The power of data gives us a new understanding of potential problems that were previously not possible to evaluate. With a growing installed base of Connected Services, we can proactively support our customers and offer them a higher level of service."
At Sicit, ConditionAlert™ has become not just a valuable asset but an essential component of their operations. With the ability to prevent major failures, minimize downtime, and deliver superior customer experiences, Sicit is confident in their partnership with Alfa Laval and the predictive maintenance capabilities of ConditionAlert™.
Highlighted technologies
CO2 savings
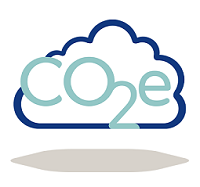
Cost savings
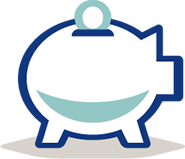