Winery in Argentina finds sustainable solution to operational challenges with Remote Support and Monitoring
In the world of winemaking, every step of the production process is vital to ensuring the quality and consistency of the final product. For a winery in Argentina, their decanter centrifuge, a key component in the production line, was facing a vexing challenge during startup. In the crucial phase, vibrations arose, setting off alarms and hindering the proper functioning of the centrifuge.
DATE 2025-02-24Fortunately, the winery had acquired the offering of Alfa Laval’s Remote Support and Monitoring, which allowed for an efficient and sustainable response to the challenge as an Alfa Laval technical expert was able to swiftly access and analyze the key performance data and alarms to address the issue.
Alfa Laval's Remote Support and Monitoring service leverages the Internet of Things (IoT) to provide technical expertise for remote monitoring and analysis of the decanter's performance.
The first step in addressing the issues was a thorough troubleshooting process and the technical expert accessed the winery's decanter data through the Alfa Laval IoT platform. By analyzing key trends for the seven days prior to the vibration alarm event, the expert was able to pinpoint the underlying cause of the problem.
The excessive vibrations were found to be caused by stopping the decanter without completing a proper flushing sequence. This finding led to a clear recommendation from the Alfa Laval expert: the winery needed to clean the decanter bowl by flushing it at high and low speeds. Armed with this knowledge, the winery implemented the recommended cleaning procedure.
The results were remarkable. After cleaning the decanter bowl as advised, the winery experienced successful start-ups without any further issues. The Remote Support and Monitoring solution proved to be a prompt and effortless solution for the winery, offering benefits that went beyond just addressing the immediate challenges.
By avoiding the need for an onsite visit from a field service engineer, the winery saved both time and money. The remote access to technical expertise provided by Alfa Laval minimized production downtime and enabled faster restarts. This led to increased overall uptime, ensuring a near-continuous production process with no loss of products or wastage of raw materials.
The winery's successful utilization of Remote Support and Monitoring not only enhanced its operational efficiency but also showcased their commitment to embracing technological advancements in the industry. Additionally, it highlights the transformative power of remote monitoring and analysis, which can be harnessed to overcome operational challenges and optimize production processes.
Through this solution, the winery managed to save an impressive 291 kg of CO2 per person, underscoring their dedication to sustainable practices and their contribution to reducing their carbon footprint.
By subscribing to Alfa Laval’s connected services, wineries – and other industries – can pave the way for a more sustainable and efficient future.
Benefits of Alfa Laval’s Remote Support and Monitoring
- Monitor your decanter’s key running parameters in real-time, get operational alarms and easy access to Alfa Laval’s expertise for troubleshooting
- Data is collected and stored on the Alfa Laval Internet of Things (ALIoT) platform 24/7, where Alfa Laval service experts can access the historical log of events to assess and make recommendations
- Troubleshooting and service instructions are provided remotely, shortening the lead time, saving the expenses and sustainability impact of field service engineer travel to your site
- It’s a smart, powerful and simple way to support your decanter’s uptime and productivity
Highlighted technologies
CO2 savings
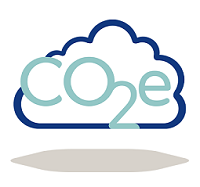
291 kg CO2 savings per person