Yeast producer raises performance levels with ConditionAlert™
Sometimes it can take time to truly see the added value of a service but after five years of subscribing to a world-class equipment monitoring system, the benefits for one European yeast production company are strikingly clear.
DATE 2025-05-12
ConditionAlert™ is a digital subscription service supplied by Alfa Laval to monitor the condition of its customers’ disc-stack centrifugal separators. With real-time insight and early warnings, it represents an investment in ensuring maximum uptime in operations.
One customer producing yeast for the baking sector was looking for peace of mind and certainty in their operations, and has been delighted with the results as ConditionAlert™ has offered expert oversight of their equipment – proactively monitoring separator condition and sending immediate alerts if any maintenance action is required.
Oskar Ohlfeldt, Alfa Laval’s Service Portfolio Manager, says: “The customer saw a need for ConditionAlert™ because they wanted to be very exact when it came to servicing their equipment and they also wanted to have as high an uptime as possible. They were an early adopter of the ConditionAlert™ concept and have been part of the development of the technology. It has been a real continuous partnership. This is vital because by working closely we can achieve optimal results and ensure that we are delivering what the customer wants.”
Previously the yeast business had to stop production for four days every year for maintenance, which meant high repair costs and continuous demand for spare parts. In the last three years alone with ConditionAlert™, they have slashed those maintenance costs, and the number of spare parts required, in half, while doubling the period of time without a service from one to two years. Now, instead of 20 days of downtime over five years, they experienced only 10 days over the same period, which corresponds to a saving of around 400,000 euros over five years.
Oskar says: “ConditionAlert™ has provided great peace of mind for them because they don’t need to make the decisions themselves on when they should service their equipment, and having a service every two years instead of one means they are able to run their batches – which are very expensive – for longer with the confidence that their equipment is running optimally.
“From our perspective, the technology gives us valuable data to base recommendations on, and has led to us offering the advice that intervals between services could be increased from one year to two years, which was great news for them, so they can be proactive, and coordinate service accurately.”
The business produces 220 cubic metres of yeast every day and ConditionAlert™ was implemented on three FEUX512 separators. The ConditionAlert™ sensors were placed on the separator bearings, and over the last five years have transmitted data points from vibrations, which are collated into a comprehensive data file and then analysed by Alfa Laval experts. Any unusual results are investigated and a tailor-made quarterly report is compiled for the customer, advising them on equipment performance and the optimal service window to maintain it.
It is user-friendly and interactive for the customer, who can see how the machine is running from the control panel on the separator but also directly on their phones via an app and also via computer through a portal.
ConditionAlert™ is now making a difference for hundreds of Alfa Laval customers in a number of different sectors, including edible oil, brewery and life science, and is tailored for each customer’s needs.
Oskar says: “We have a service agreement with our European yeast producer based on ConditionAlert™ and that shows a commitment from both ourselves and the customer, emphasizing the added value that constant monitoring adds by extending the lifetime of the equipment. Ultimately, the better you service your equipment, the better it performs and the longer it lives and that is what ConditionAlert™ is all about.”
Highlighted technologies
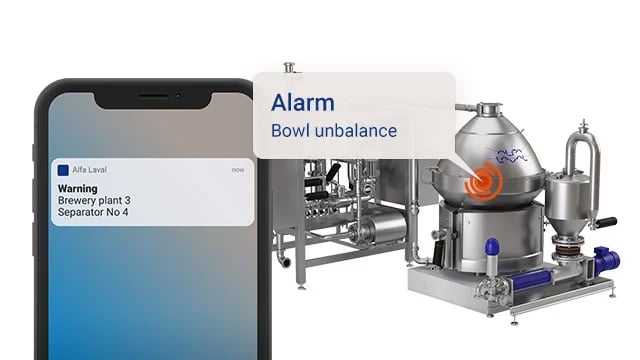