Alfa Laval WideGap: strong collaboration leads to energy-saving success in beer column integration
Saving energy was high on the agenda when a small European ethanol producer approached Alfa Laval with an idea for a process adaptation at their new plant in Serbia.
DATE 2025-02-24Etanol Lab, based in Sabac in western Serbia, wanted to implement an innovative modification: integrating the beer column with a rectification column using Alfa Laval’s plate heat exchanger technology as a beer column reboiler.
Alfa Laval’s WideGap heat exchanger was selected as the optimum technology for this duty being the only heat exchanger, which can accommodate whole stillage on one side with particle size up to 6mm, and boiling in the unit.
The initial design looked promising on paper but cru[1]cial to the successful outcome was the collaboration between the two companies in developing an optimally performing, customized solution.
“The customer approached us when they were building the plant,” Global Technology Application Process Engineer Dimitrije Djordjevic explains. “They wanted to save energy with this rectification column and they knew that if they connected it to the beer column in a certain way, it had the potential to reduce energy consumption. We knew theoretically that it would work but we were concerned about fouling.”
In co-operation with the customer, Dimitrije devised a series of industrial-scale tests and by making small adjustments to the design, he developed a low-fouling solution that achieves a low temperature difference between the hot and cold sides, and impacts positively on the overall energy efficiency of the plant by reducing the new energy-input requirement by as much as 30%.
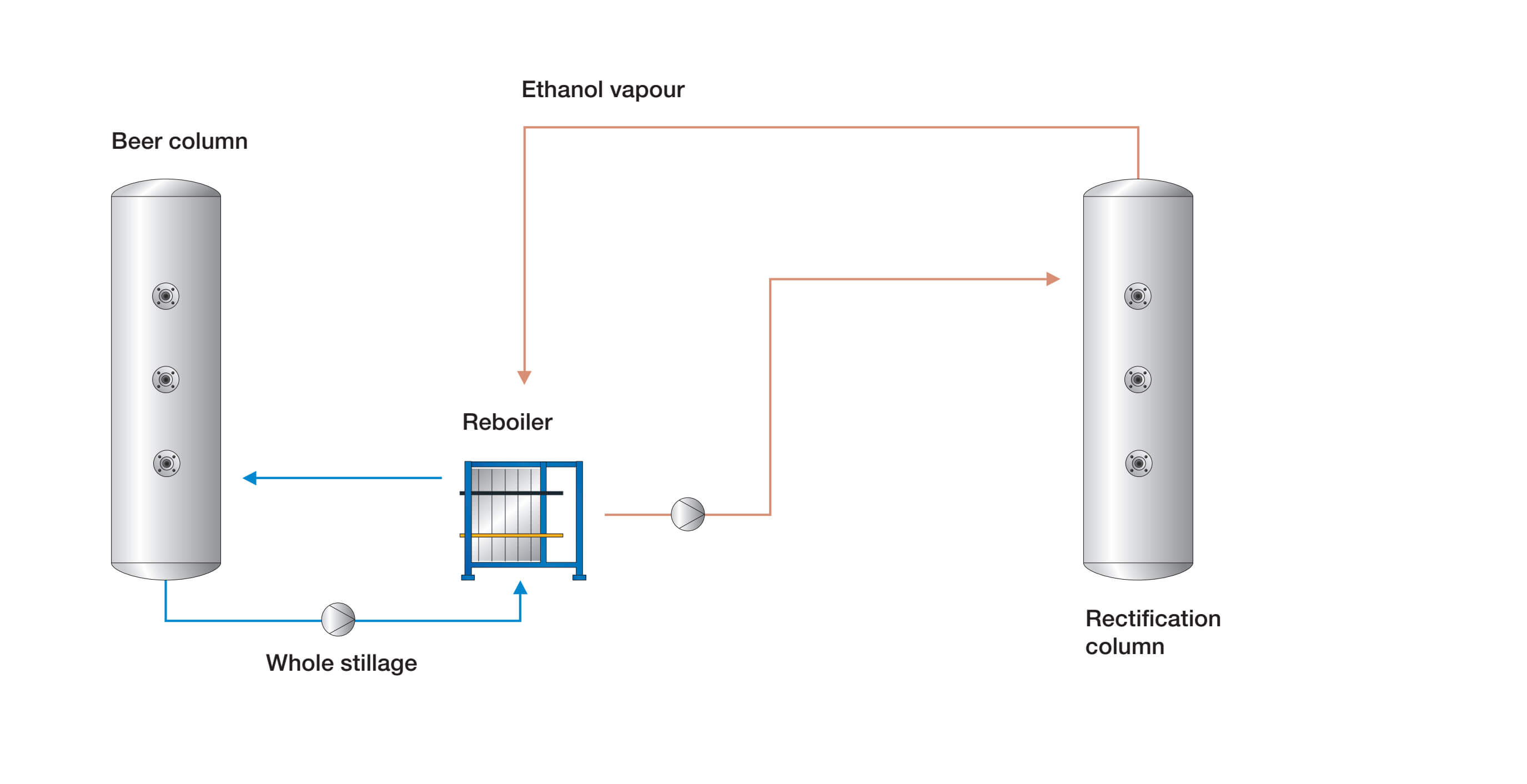
“We worked with the customer on the complete system,” says Dimitrije. “We had a theory. We got some lab-scale proof and then we designed an industrial unit – modifying both the heat exchanger and the system as a whole until the customer was happy.”
The minimal fouling inside the WideGap heat exchang[1]er enables stable performance and extended cleaning intervals. For Etanol Lab, this was an added bonus: “We’re a small business and cleaning-in-place is a costly procedure. So, being able to go three months between cleanings is a big win for us,” says Dejan Džagić, owner of Etanol Lab. “The unit has been running for a year and a half now, and we couldn’t be happier with its performance.”
Working in collaboration with customers like this demon[1]strates how Alfa Laval is on-hand with the expertise to help customers develop the optimal solution for their business needs
“Now we have the knowledge, we can implement this solution with other customers who have this problem, but not only that, this demonstrates that we are a company that has the knowledge to build customized systems based on the specific needs of ethanol producers – a company who will listen to the customer to understand the problem and then we will work with them until we find and can implement the right solution for their business,” Dimitrije concludes.
Highlighted Technologies
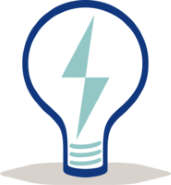
Energy saving of new energy-input by 30%
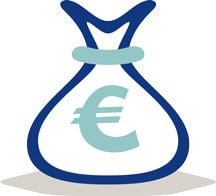
Water savings due to longer cleaning cycles
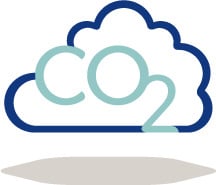
CIP every three month instead of every day
Tags
All