Commitment to data-driven optimization sees Alfa Laval’s Eskilstuna team halve water consumption
Alfa Laval’s Eskilstuna factory in Sweden represents a textbook example of walking the sustainability talk and the latest initiative launched there by the real estate, quality and environmental team has saved thousands of cubic metres of water.
DATE 2025-03-20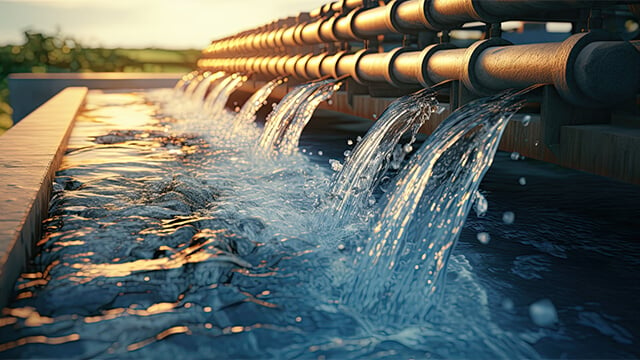
The facility, near Stokholm, manufactures high-speed separators, and hosts 250 workers and around 50 standalone machines across its 20,000 sq m. It is a process heavy on water and energy use, but one rich in potential when it comes to identifying opportunities for saving resources and aligning with Alfa Laval’s strategy of reducing scope 1 and 2 emissions.
The Eskilstuna team were eager to mine this rich seam of opportunity and when it came to embarking on this particular sustainability journey there was only one place to start – measurement.
Operating from a belief that “to measure is to know,” the team understood that to be clear about how much water was being used and where they needed to start off by monitoring and measuring water use around the factory.
In fact, what the measurements were showing was that water consumption at the factory was on the increase. By digging deeper and mapping the water consumption in production, the team discovered that a significant amount of this consumption from the city water supply line was connected to one particular standalone machine, a 3D printer in the technology development area of the factory.
Once the team had identified the machine, it was disconnected from the city line and reconnected it to the geothermal heating system for cooling and heating. The heat pumps were then configured so that it could manage the temperature levels. That means the printer is now in the closed loop system and the use of city water has been brought to zero.
This one change has cut water consumption at the factory in half, saving 4,000 cubic metres of water a year.
It is this commitment to digging into the detail that is at the heart of the sustainable success story at Eskilstuna. Comprehensive data is gathered, and tweaks are made to save on resources, be it water, energy or electricity.
“We have a system in place that measures water, energy and electricity consumption,” says Daniel Berton. “We have really focused on the heating systems and water consumption recently, and we now have two meters on the pipes to the site so that we can do more measurement and set up alerts if consumption is increasing and map and identify which areas and lines are responsible.”
The results build on striking improvements the team had already made in cutting electricity use, where the installation of ex motion-activated lights and small ventilation adjustment has cut consumption by almost 5%. The next major project being looked at is the recovery and re-use of heat in the ventilation system and the use of smart motors and fans.
“These wins motivate the whole team,” says Mikael Bylund. “It can be a challenge to manage change but once people see the impacts it becomes easier. People might think it’s a huge mountain to climb, but like every journey, this is step by step. Start with the little things and keep on measuring and fine tuning.”
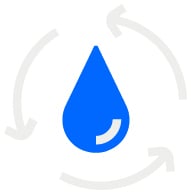
Reuse of 4,000 cubic meters or 4 million liters of water.

50% reduction in water use.