More plant-based protein: The mother of inventions
With global protein demand on an upward trajectory and the world’s population projected to expand considerably by 2050, innovative solutions and advances in technology will be key in developing sustainable sources of protein to stabilize future food security. It will require new thinking and innovation to produce up to 70 percent more food by 2050. (UN, 2019).
DATE 2024-11-20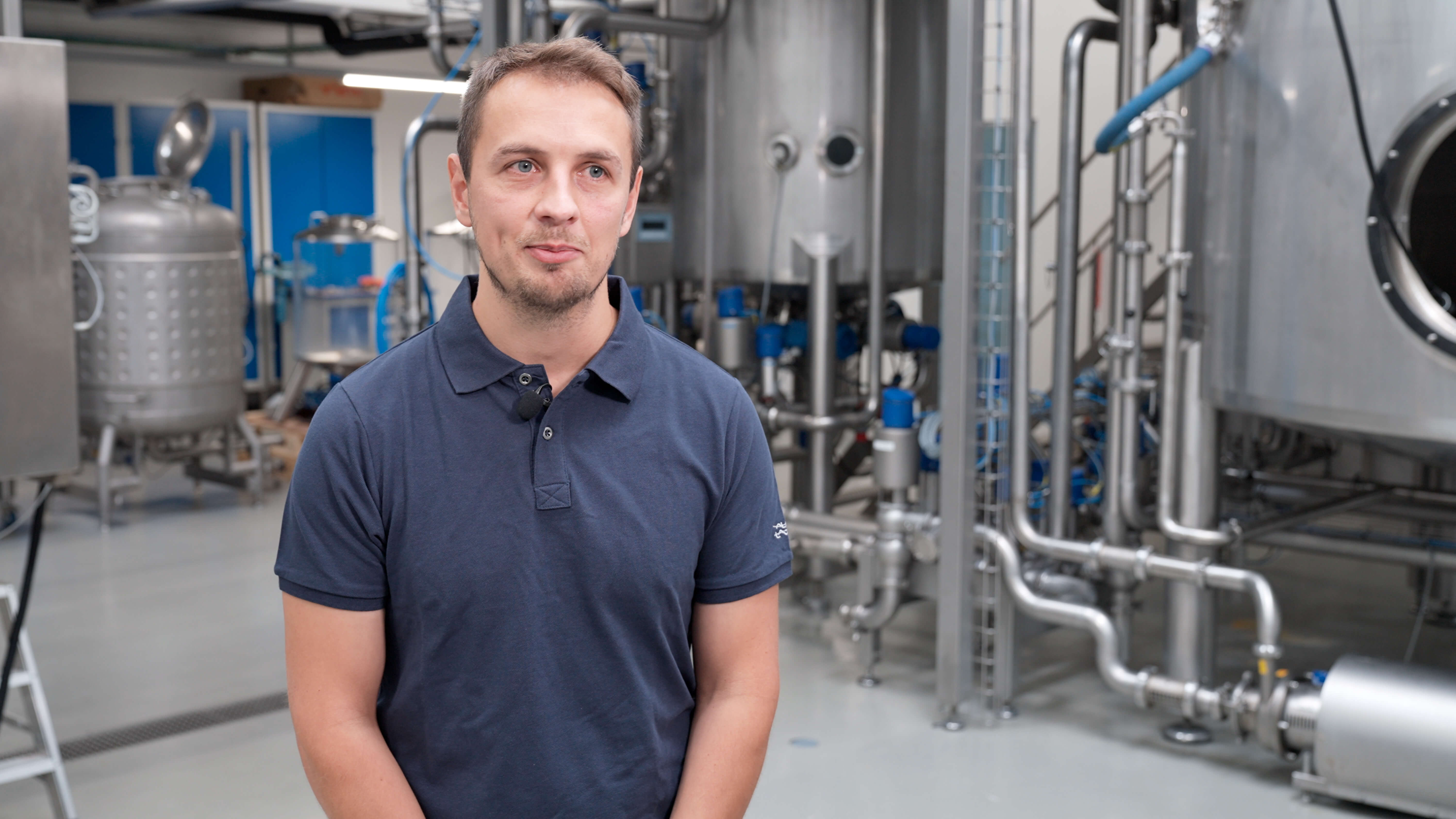
Plant proteins are set to be a major part of the solution. They cost less to produce than animal proteins and have a smaller environmental footprint. However, they present specific challenges to processors due to their relatively poor solubility, foaming, emulsifying and gelling properties.
Traditionally, Alfa Laval’s decanters have been the go-to technology when it comes to separating out plant proteins but the structure and resulting behaviour of the proteins inside these machines makes this process comparatively inefficient; with big decanters and low flow rates required to produce protein isolates of sufficient quality, and unavoidable product losses.
Ironing out production inefficiencies will be crucial going forward if the ever-increasing demand for healthy plant-based proteins is to be met; and for Alfa Laval, this represents a huge opportunity for innovation and process optimization.
Step forward Alfa Laval’s Global Sales & Technology team in Agro & Protein Systems who, with the support of a leadership that welcomes problem-solving and encourages new ideas and innovation, have developed a more energy-efficient processing system, which produces higher protein yields of better quality at lower operating costs.
Launched in April this year and currently the subject of a patent application, Alfa Laval’s new Plant Protein Separation System has been developed by Process Engineer Joosep Masik and his colleagues, and was born out of a determination to be more competitive in the market.
“Essentially it all started from frustration,” Joosep explains. “We were disappointed that our protein separation systems were becoming expensive because we had to use two decanters and it didn’t seem as though we had a competitive offering for the future. We wanted to come up with something unique to differentiate ourselves in the market.”
Galvanized by the supportive environment and can-do culture, the team set to work. Brainstorming led to lab testing and confirmation they were on the right track. A more extensive feasibility assessment followed at Alfa Laval’s test centre in Kolding, Denmark, until the team were satisfied, they had the right solution and the new Plant Protein Separation System was born.
“This problem really got our creative juices flowing and at the start there were a lot of ideas,” says Joosep. “Eventually it turned out that the solution had already existed in Alfa Laval for a long time – it was a disc-stack centrifuge called Alfa Laval TopStream™.”
By incorporating the TopStream disc-stack centrifuge into the process for the primary separation phase with a wash decanter carrying out the secondary separation phase, the team were able to increase the production capacity and quality of the protein isolate while also reducing energy consumption and overall operating costs.
“With this system we have maximized the potential of both machines,” says Joosep. “The TopStream has higher throughput and greater separation efficiency, but the decanter is an essential last step – delivering a drier product and minimizing product losses.”
Management support was key to the successful development of the new Plant Protein Separation System. Time, resources, and space in busy schedules were carved out to facilitate progress.
“Once we had come up with the idea, we needed to prove it could work,” says Joosep. “At that point I had to take it up with my managers because we needed time and resources. It was a huge leap of faith, but they gave us the approval to do the tests we needed to do. We did two tests. The first one proved it could be done and the second one established how we could fit it into our solution. We couldn’t have done with it without the backing of our managers.”
As well as increased yields, higher throughput, gentle product handling and continuous solids output, the Plant Protein Separation System is also more energy efficient. The TopStream disc-stack centrifuge has a much lower power consumption compared to conventional production methods.
“Essentially this is a more sustainable solution because less power is required but we also believe the new system will result in much leaner installations, requiring less stainless steel to produce, which is another obvious benefit that enables us to reduce the carbon footprint of processing,” says Joosep.
And from a job satisfaction perspective, being given the go-ahead to explore ideas with colleagues and develop a positive solution to a potentially market-limiting problem has been very rewarding.
“One of the coolest things about my job is that we are encouraged to think about innovative solutions for the future,” says Joosep. “Obviously, if you want to be innovative you have to take some risks but there can be huge returns and in this case, we have made the most of a unique opportunity to be pioneers in this area.”