More with less: olive oil production in Greece
When the Anagnostopoulos family looked to improve olive oil production and energy efficiency at their two olive oil mills in Greece, their trusting relationship with Alfa Laval and confidence in Alfa Laval's technology and technical expertise were key.
DATE 2025-01-24Five generations of the Anagnostopoulos family have been producing extra virgin olive oil since 1896, from Koroneiki olives sustainably grown by local farmers in the Southern Peloponnese-Messinian countryside, using only natural rainfall for irrigation.
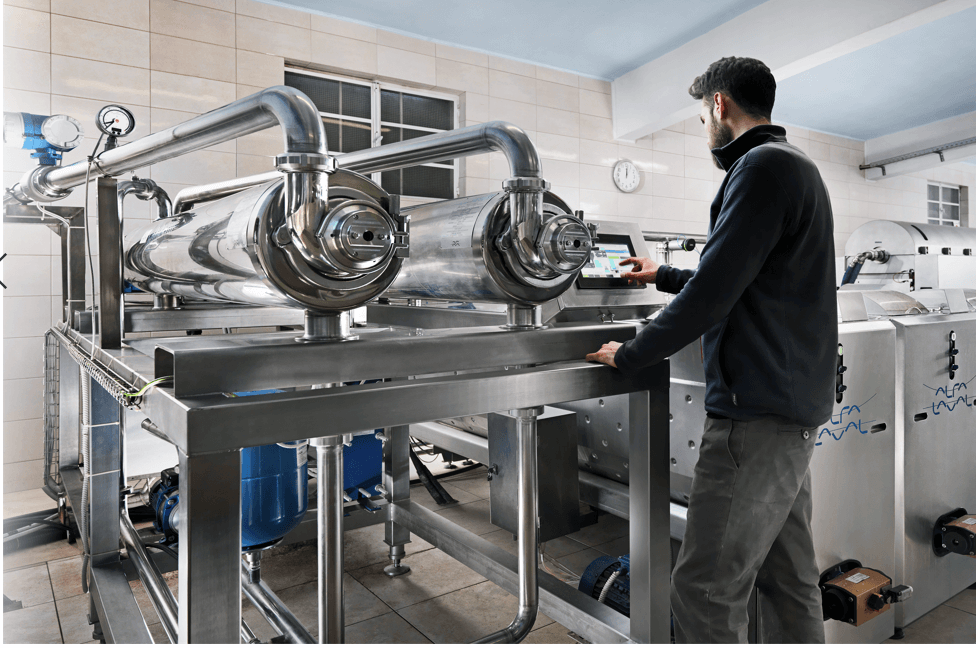
Owner of the OneOlive olive oil mills, Dimitris Anagnostopoulos.
Innovation at its best: a fast process that reduces the malaxation time by half
The One & Olive company’s focus on innovation and quality is strongly underpinned by its sustainable olive oil production methods and a firm commitment to improving energy efficiency and reducing carbon footprint.
This approach has been supported for many years by a long-standing relationship with Alfa Laval, which has enabled the company to advance in olive oil production methods; most recently, using Alfa Laval Contherm Scraped Surface Heat Exchanger to improve energy efficiency while reducing energy consumption in the processing of the Koroneiki olives.
“This advanced technology guarantees the least contact with oxygen during the production process while delivering fresh olive oil in less than 18-22 minutes,” says Dimitris Anagnostopoulos. “After the olives have been sorted, washed and crushed, the temperature is homogenized in less than one minute without any contact with oxygen.”
The paste is then gently heated to 27°C before heading for centrifugal separation in an innovative process that heats the paste very fast in just 30 seconds compared to the traditional method
“We are among the first companies using this method globally – gaining reduced contact with oxygen, increasing the high quality of our oil and making the process more efficient, while also reducing energy consumption,” Dimitris continues. “By doing this, we are promoting sustainable production processes for the next generations – minimizing our impact on the environment and gaining a reduction in carbon footprint.”
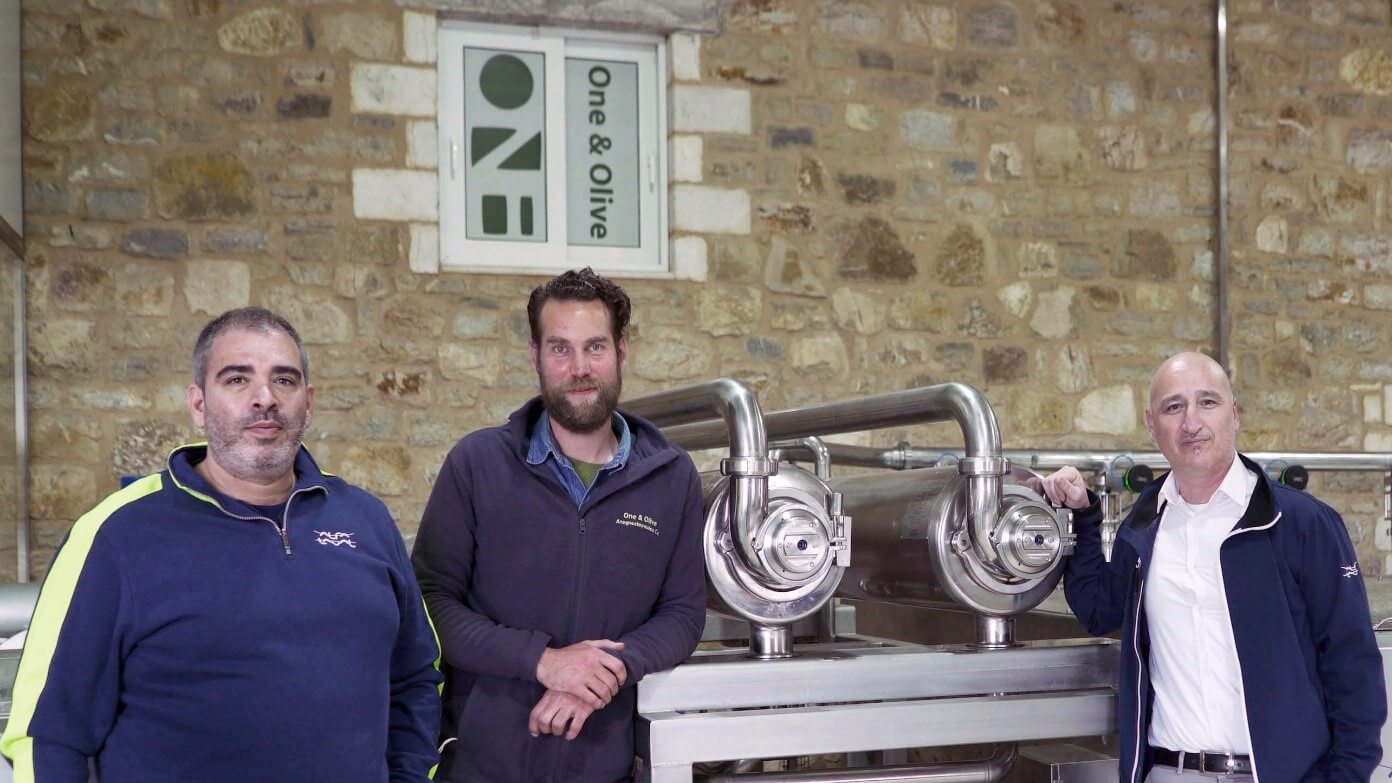
At the customer site from left: Alfa Laval field service engineer Vassilis Michalakakos, owner of the OneOlive mill Dimitris Anagnostopoulos and Regional Sales Manager for Food & Water applications in Greece, Konstantinos Axaridis.
No longer heating the environment – 15 percent gain in energy efficiency
Alfa Laval’s Regional Sales Manager Konstantinos Axaridis and Field Service Engineer Vassilis Michalakakos began working with Dimitris in 2015 to establish how production processes could be optimized – tapping into the expertise of Contherm colleagues in the US when required.
A series of on-site test runs using Contherm technology proved that the process was faster with higher quality oil, explains Konstantinos, adding: “The increased quality of the end-product and faster process gave Dimitris differentiation from the competition, and he gained more customers.”
“With the Contherms, we can run at more than 12 tonnes per hour – and without any problems related to working at high pressure because it’s a very gentle process,” adds Vassilis. “Also, there is a 15 percent gain with respect to the energy efficiency of the process. With the old process, there was no thermal insulation, so as well as heating the olive paste, we were also heating the air outside. Now, with the Contherms, we are not heating the environment. This means that there are many kilocalories of thermal energy that we have reduced using this system.”
The decrease in energy consumption translates into an annual energy saving of 67,400 kWh, which gives the customer a reduction in carbon footprint, measuring 52.6 tonnes CO2e.
The solution is a win-win, concludes Konstantinos. “Good results mean happy customers, which leads to more customers and a sustainable business,” he says. “The proof is in our repeat orders from other customers, and we expect this to continue in the coming years.”
The solution has proved so successful that it has now been replicated in 10 olive oil mills across Greece over six years and with a single-digit million Euros total value.
Energy savings
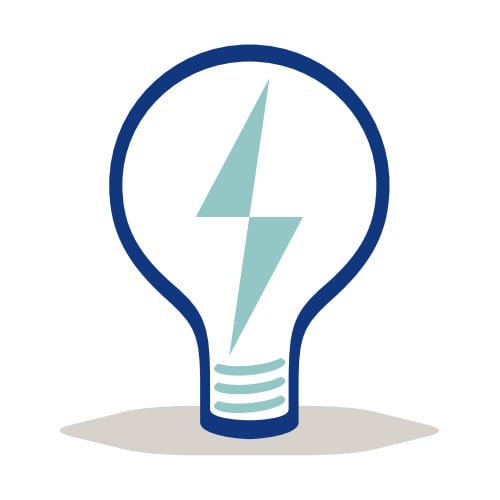
Yearly energy saving of 67,400 kWh
CO2e savings

Yearly emissions reduction of 52.6 tonnes CO2e
Reduction in energy consumption and carbon emissions
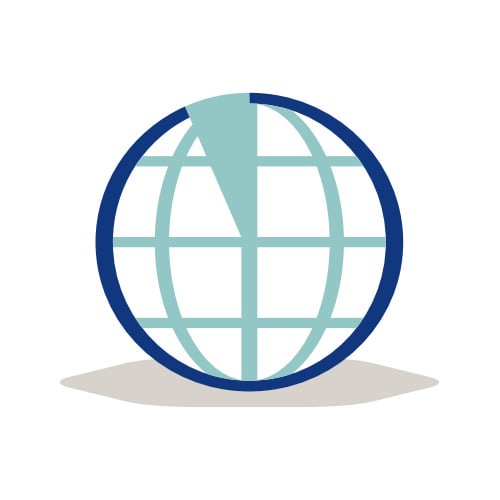
The reduction in energy consumption and carbon emissions allows producing an additional 320 tons of olive oil without increasing the use of energy and related carbon emissions.