Separator upgrade nets 30% energy savings for a starch giant
When a global agri-food giant sought to increase capacity and improve energy efficiency at its starch processing plant in Spain, they initially planned to purchase a brand-new, large-capacity centrifugal separator to replace two smaller machines.
DATE 2025-02-07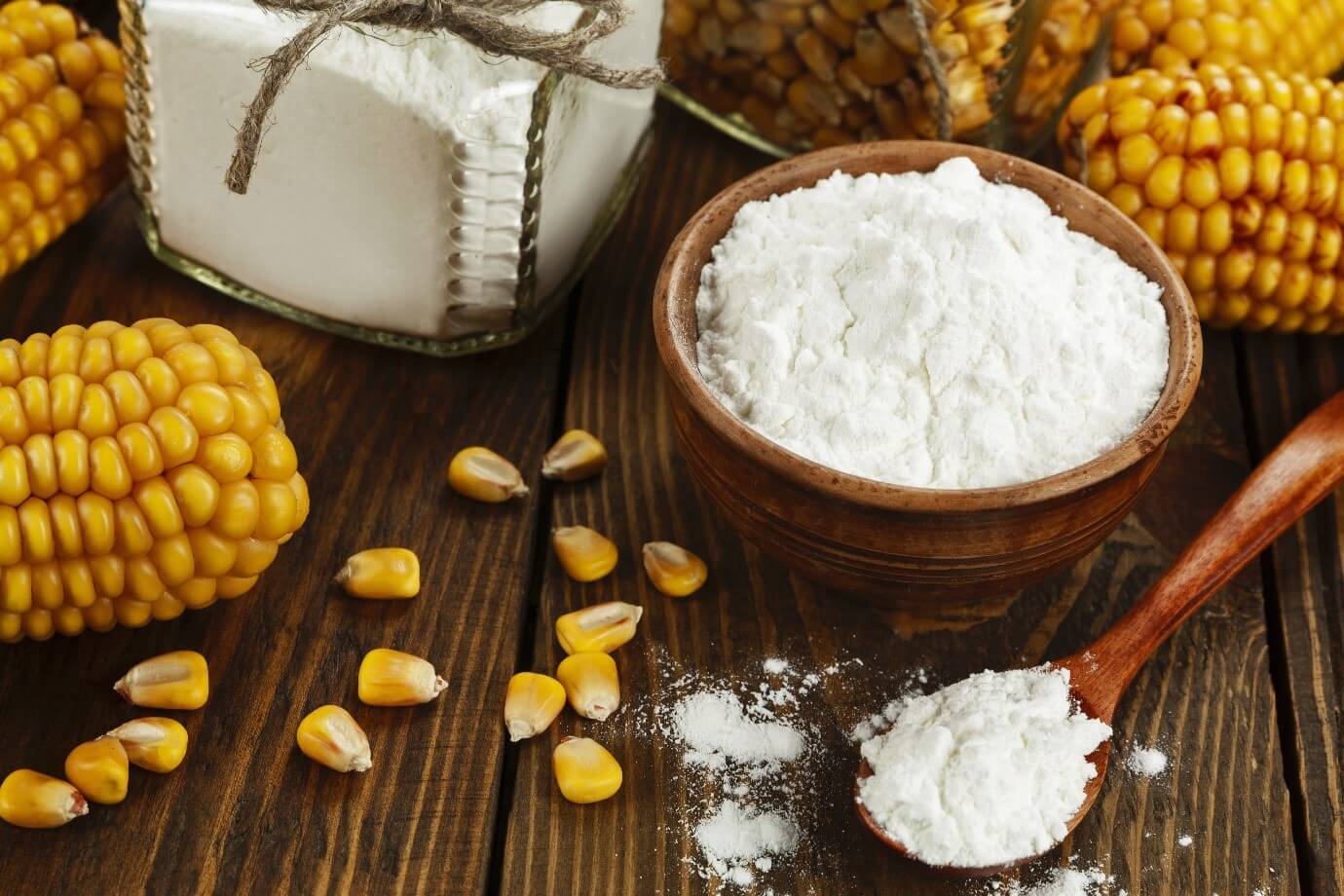
When a global agri-food giant sought to increase capacity and improve energy efficiency at its starch processing plant in Spain, they initially planned to purchase a brand-new, large-capacity centrifugal separator to replace two smaller machines.
The company bought one new machine. However, by deciding instead to upgrade the other existing Merco starch separator, the company achieved a 50-percent capacity increase while netting up to 30 percent power savings with an investment that was half the cost of the new machine.
Starch is the most common carbohydrate in the human diet and is used to thicken, stabilize, emulsify and enhance the texture of everyday foods. It can be sourced from a variety of raw plant ingredients, including corn, waxy corn, potato, tapioca and wheat.
Starch-based products have been produced in a four-stage CWT (corn wet milling) process at the company’s site, in Spain for more than half a century and today, these ingredients can be found in foods and beverages worldwide.
In 2017, before an order was placed for the new machine, the company invited Alfa Laval to assess the condition and performance of two Merco BH-30 separators, which had been operating on-site since the plant was commissioned. This led to detailed discussions over the next two years, and a decision was finally made to upgrade rather than replace.
Upgrading a Merco 30 to a 32 increases flow capacity through the machine while also reducing energy consumption and simplifying maintenance. It is a simple process on existing machines. It can be done in a minimal timeframe – an attractive proposition when production lines are run 24/7 year-round and any interruption is unwelcome.
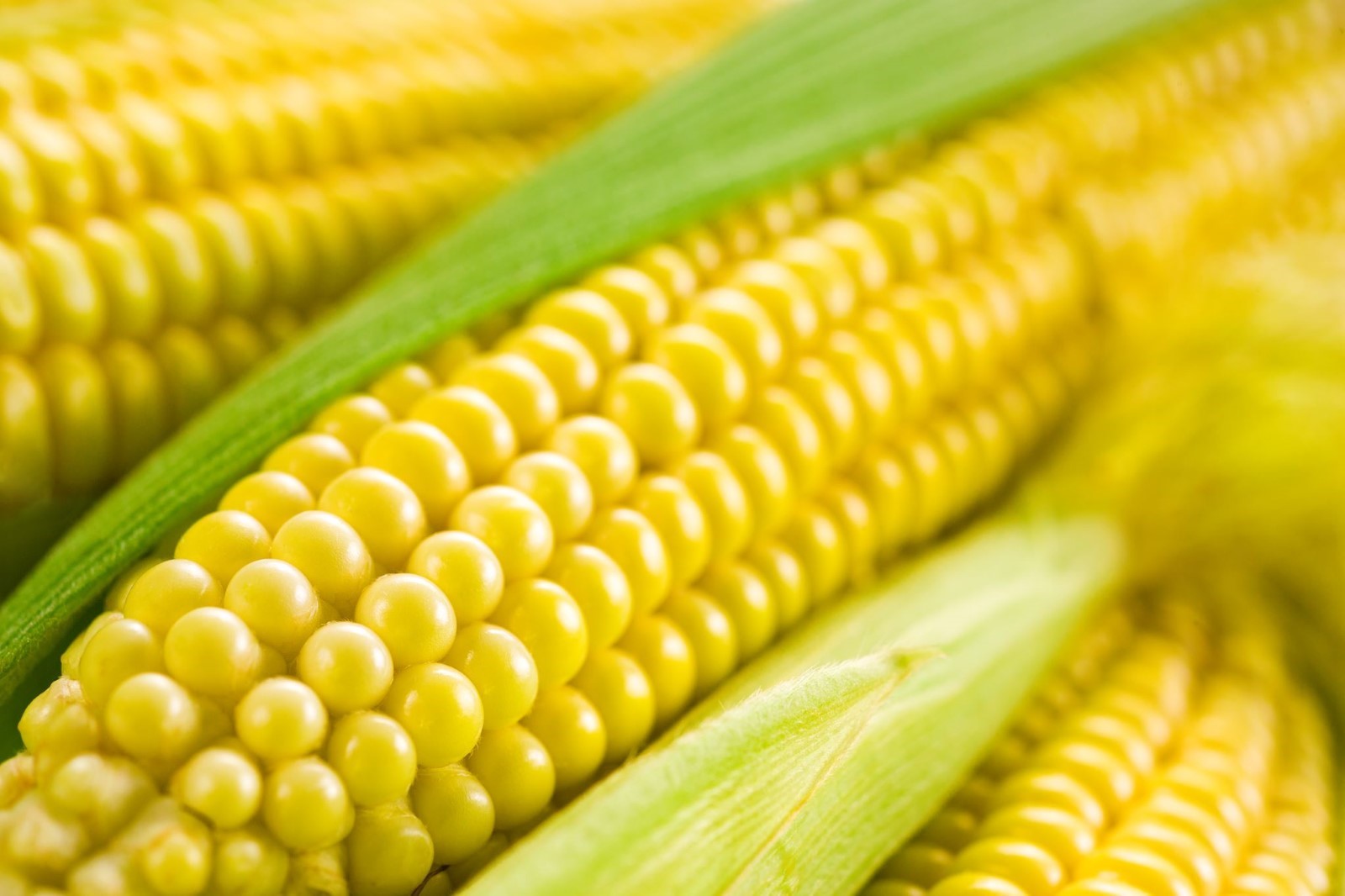
“Upgrading is the sustainable solution,” says Kenneth Gustavsson from Alfa Laval’s High Speed Separators Global Service team. “With an upgrade, we are re-using the machine frame and all the drive components and adding only a new bowl and new in- and outlets. The increased capacity for the same power consumption produces a net power saving and increased overall efficiency.”
In addition, inserting of Alfa Laval’s high-efficiency nozzles reduces the machine’s power draw by between 25 and 30 percent.
“These plants are limited in their electrical power-handling capabilities and investing in a larger electrical power-handling capability is costly and unsustainable, so any saving that can be made is welcome, and since Merco machines can save a lot of power, this is an appreciated product for the customers,” says Kenneth.
This was certainly the case for this company, and initiatives like the Merco upgrade project firmly underpins the company’s ongoing commitment to sustainable food production.
For Alfa Laval, upgrading existing equipment where possible is the most sustainable solution and a win-win for customers and the planet.
“We always consider the needs of the customer first to be really able to customize our offer depending on their needs, bottlenecks, issues and plans for the future,” says Kenneth. “In this way, we can really make a perfect match and address all the customers’ challenges and requirements in the most effective and sustainable way.”
Highlighted technologies
Energy efficiency
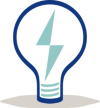
30 percent energy efficiency gain
Upcycling
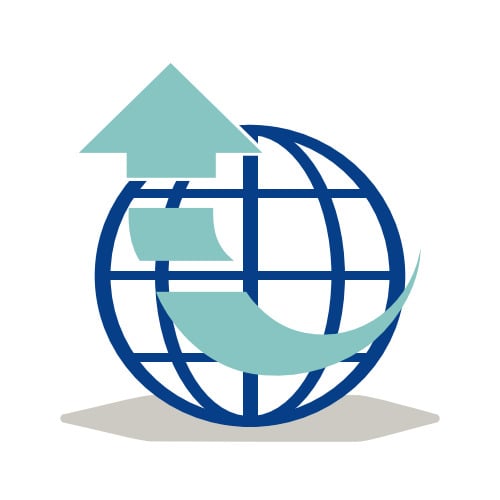
By upgrading existing machinery, the customer has, in effect, achieved an upcycling result: They have turned machinery which was earmarked for disposal into a piece of machinery to secure a 30-percent energy reduction.