Water recycling solution generates EUR 30,000 in cost savings for world-leading biosolutions business
With the global population set to grow to 9.7 billion people by 2050 (UN, 2024), and ever-changing and growing consumer demands and economic climate shifts, a biosolutions giant headquartered in Scandinavia helps food and beverage producers around the world generate more from less, supporting their processes to be more sustainable and efficient.
DATE 2025-03-20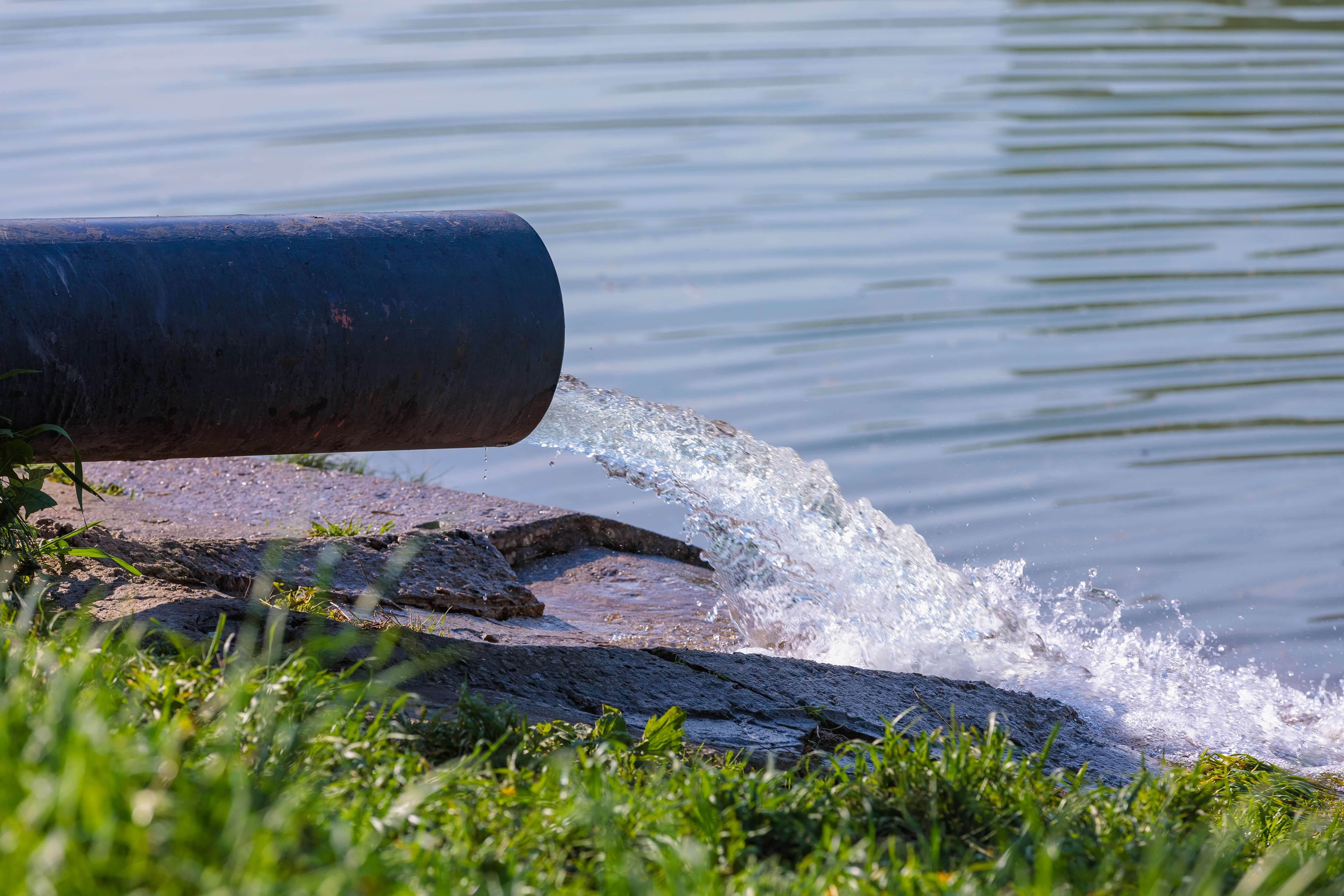
Their facility at Tianjin in China makes enzymes for use in food and beverage applications as well as enzymes for washing powder detergents – all of which are water-intensive processes. It is here that a solution from Alfa Laval is opening the door to significant water reuse and savings, boosting sustainability and profitability – and helping the company lead the way in this vital area.
Alfa Laval’s Aldec decanter has been incorporated into the wastewater treatment process – supporting the company in delivering for its customers while meeting its robust sustainability targets and saving around EUR 30,000 a year in new water costs.
King Li, sales engineer, is a key member of the Alfa Laval decanter team in China, and he explains: “The enzyme production generates a lot of wastewater that requires treatment before it is discharged or recycled. The decanter dewaters the sludge, cleans the wastewater, and then goes through RO treatment (reverse osmosis) so that the water can be reused in the plant for cooling and other operations. The only thing you can’t do is drink it.”
“Water in China is expensive, and Government regulations are looking to drive reuse and recycling, so this solution is at the heart of meeting those regulations and boosting the company’s sustainability performance at the factory.”
The efficiency and speed of this new decanter see a significant volume of water passing through – around 25 cubic metres an hour – and this means that the bacterial waste sludge from the enzyme production process – or ‘cake’ – is much drier, with 8 percent less water. Over time this reduction in volume helps reduce transport costs and environmental impacts – another sustainability benefit.
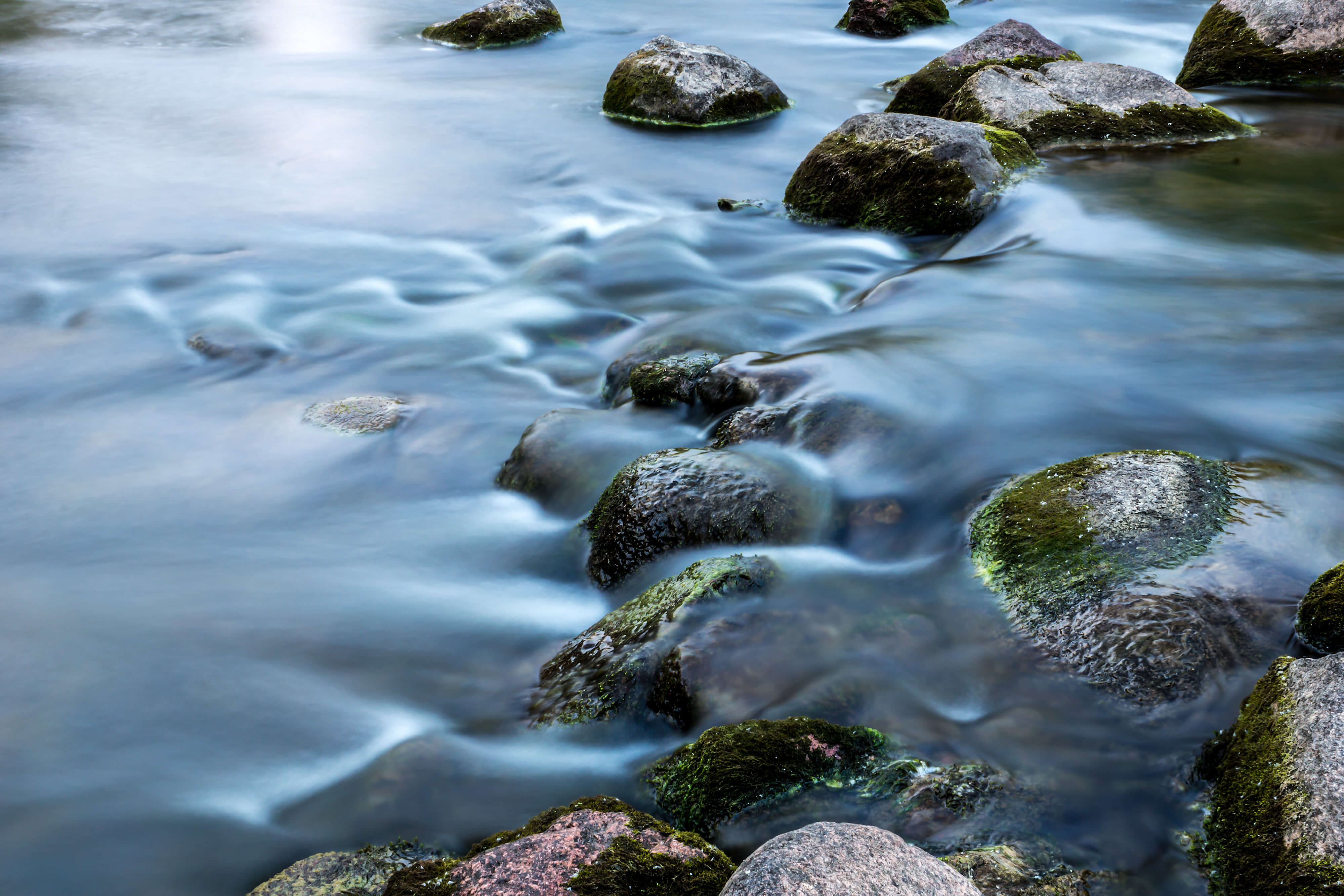
The company was a merger of two existing companies, and Alfa Laval’s long relationship with the companies has been a key part of the success of this latest project. Throughout the process, Alfa Laval has focused on communication and cooperation before, during, and after the installation of the decanter at the end of 2023.
King Li said: “We have had very good cooperation with the customer over the last 10 years, and we have worked very closely with them before, during and after the installation to ensure that they receive maximum benefit from the Aldec. In terms of sustainability, they wanted a decanter that would not be phased out in a short time and would have good wear protection in the feed zone, and the Aldec meets both of these requirements.”
This included regular visits from decanter process specialist Tim Mikkelsen, Global Technology Business Development, BU Decanters, based in Denmark, to ensure that the decanter and other Alfa Laval equipment at the factory are operating to maximum efficiency.
Representatives for the biosolutions company were invited to a tour of Alfa Laval’s factory in Kunshan, China, where the Aldec is built so that they could see the quality of the product up close and talk directly to the people making it. The machine upgrades the fully wear protection in the feed zone part to solve the pain point from Aldec.
Confirming the order was followed by extensive planning meetings and training to ensure a thorough and comprehensive commissioning process with the customer.
King Li said: “This shows that we are not just an equipment supplier but also a partner for the lifetime of the equipment. We are always ready to help our customers operate profitably while hitting their sustainability targets.”
Let’s make the most of it: unlocking the value of wastewater
Highlighted technologies
Annual water savings at 40,000 m3 gives a cost saving of EUR 20,000.
Higher cake dryness – i.e., less water in the waste – has reduced waste transportation by trucks and costs by EUR 10,000 a year.