WideGap heat exchanger solution taps into the energy-saving potential of waste heat recovery
Capturing the energy from the vapour coming from the DDGS dryer in the final stage of the ethanol production process has enabled one producer in Australia to reduce overall energy use, save money and increase the sustain ability of their operation. The company was keen to recover the heat that was being discharged to the atmos phere during the drying process. This process completes the production of dried distillers grains with solubles (DDGS) – a valuable by-product of ethanol manufacture.
DATE 2025-02-24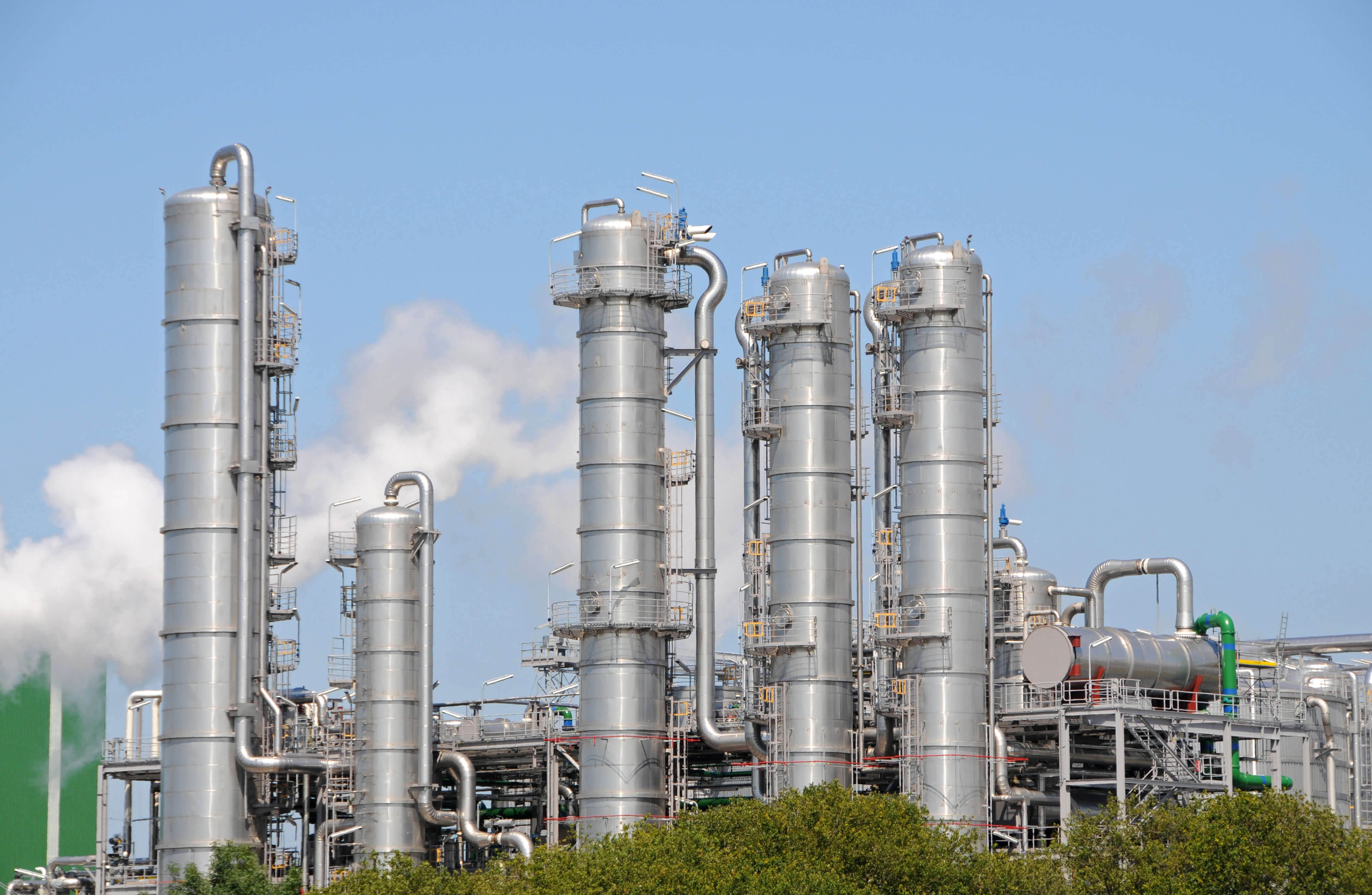
In collaboration with Alfa Laval, the company opted to install three WG350S WideGap heat exchangers – two in operation and one on standby – to capture and condense the water vapour released from the dryers so that the resulting hot water produced can be used elsewhere in the ethanol production process.
“The installation of the units, due to be completed towards the end of this year, will enable the recovery of 7392 kWh of heat per hour in the form of 90°C hot water, which will be used as a heating source in several heating duties in the ethanol production process,” explains Eser Aydin, Senior Global Technology Application Process Engineer at Alfa Laval. “This will reduce the need for live steam in these duties and reduce the plant’s overall energy consumption.”
Alfa Laval’s WideGap plate heat exchanger technology is particularly suited to capturing heat from dryer vapour, says Eser: “We can configure a design with a very low pressure drop that will not disturb the drying process. We are producing 90-degree hot water with 93-degree vapour. This three-degree difference can only be achieved with plate heat exchanger technology, and this is impor[1]tant because the warmer water you have, the more useful it is and the more options you have, to use it in other processes that have heating duties.”
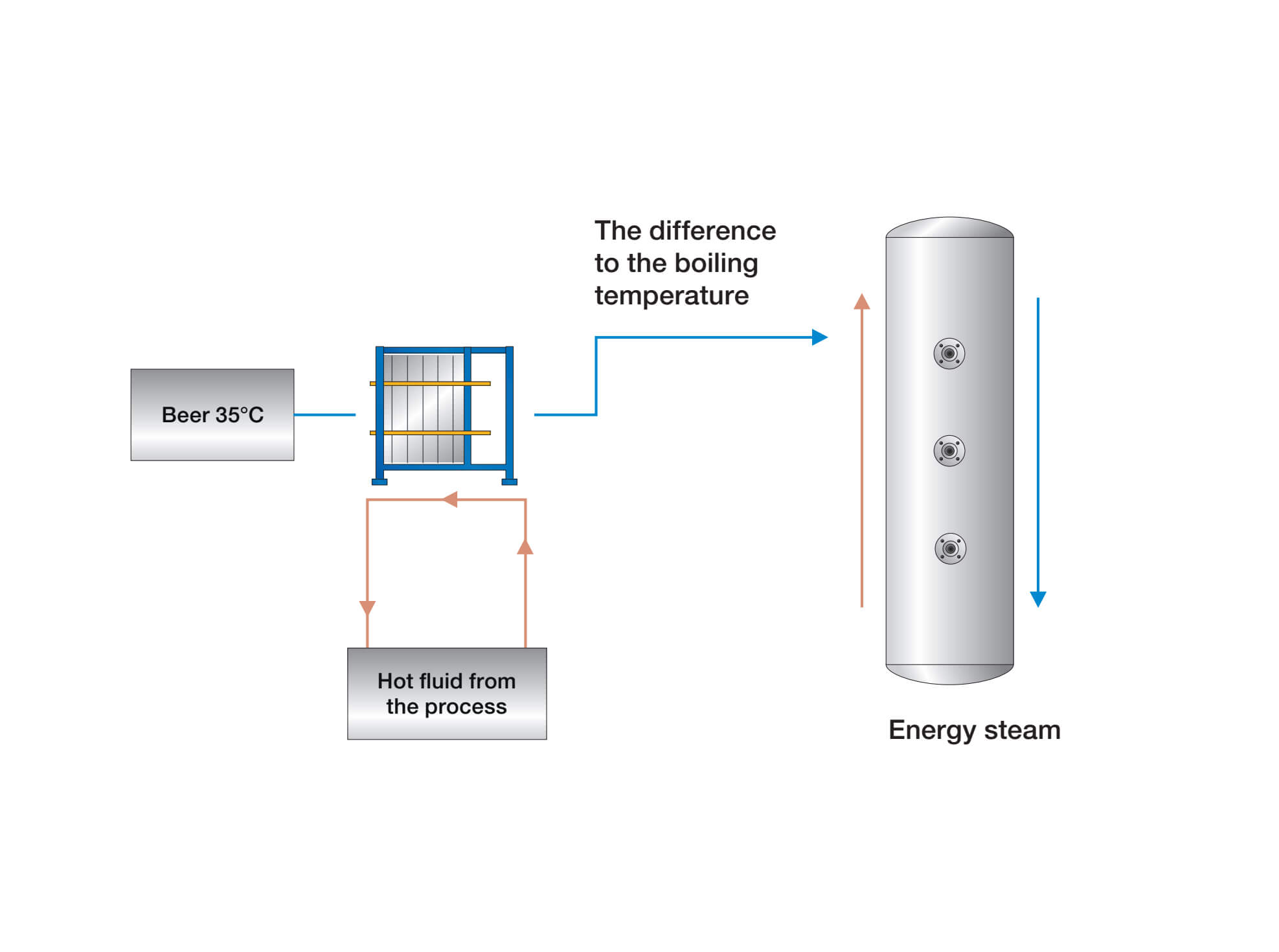
Eser concludes that using this technology to capture waste heat is an attractive option for ethanol producers looking to save energy, cut costs and increase the sustainability of their operation.
“With plate heat exchanger technology there is an op[1]portunity to turn the waste heat from dryer vapour into usable energy,” he says. “For plant managers, reusing energy that was previously released to the atmosphere could turn out to be a gold mine!”
The ethanol biorefinery – opportunities
As the focus continues to sharpen on capitalizing on opportunities to increase profitability by extracting saleable products from what was previously considered waste in industrial processes, ethanol producers are looking more and more at the re-utilization both ethanol and more importantly the by-product from corn- or wheat-based ethanol production, to produce value-add[1]ed products. These include a wide range of bulk chemi[1]cals, fine chemicals, oils, plastics, solvents, protein, and fibres but some of the most valuable products extracted from the by-product are corn oil and protein. It is pos[1]sible to extract relatively small quantities of these from the by-product, but with a significantly higher value than the ethanol itself. Apart from improving profitability for ethanol producers, this also reduces the footprint of the production as it is possible to produce more from less.
Highlighted Technologies
Energy savings
Energy saving 7400 kWh
Payback time
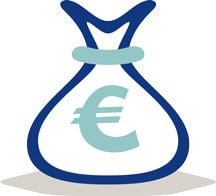
Payback time less than half a year
Cost saving 6000 EUR/day
CO2
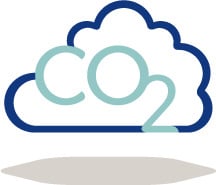
9,250 tonnes CO2 e emissions/year