Wort cooler uplift nets major energy savings for UK brewer
Upgrading heat exchanger to boost sustainability One of the UK’s largest breweries has boosted its sustainability drive thanks to upgrades on two plate heat exchangers for wort cooling that have delivered significant energy, water and CO2 savings
DATE 2025-03-07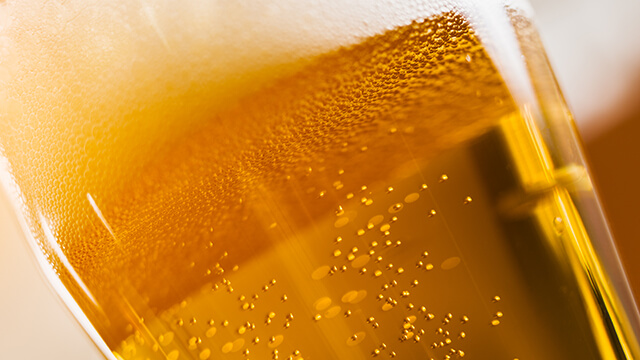
The large brewery in the north of England prides itself on focusing on the sustainability of its operations, which produce millions of pints of beer a year, and this latest upgrade has delivered savings of 195kW per hour of operation, 8000 litres of water per brew and approximately seven tonnes of carbon dioxide a year.
The brewery had targeted efficiencies on the glycol circuit to reduce energy consumption for cooling and to achieve this they turned to Alfa Laval for support to review the opportunities. Together they identified the potential to increase the efficiency of the wort cooler.
Paul Heppenstall, Technical Product Support Engineer for Alfa Laval, says: “The company uses a number of our products and is a long-term customer of ours. These heat exchangers had been operating in place for a number of years, they trusted them as Alfa Laval technology, and they wanted to look at the possibility of keeping them running rather than buying new equipment.”
The local Alfa Laval team stepped in and worked closely with their brewing partners to redesign the units and, following installation in 2023, their performance level has leapt by six percentage points, delivering that 195kW per hour saving along with a reduction of 80 hectolitres of cooling water per load. These eye-catching savings are supporting the brewery in reaching its ambitious sustainability targets, especially as this is an area where the company has put a strong focus, in an industry which is intensive in its water use.
“They wanted us to look at upgrading the heat exchangers to be more energy efficient and create more heat, and to do that we went back to basics,” says Paul’s UK colleague Colin Morgan, Product & Application Manager. “We looked at the original specification and what it was designed to do, compared to what it was actually doing – and we found that those two things were quite far apart. We needed to know why that was happening and whether it was being used correctly.
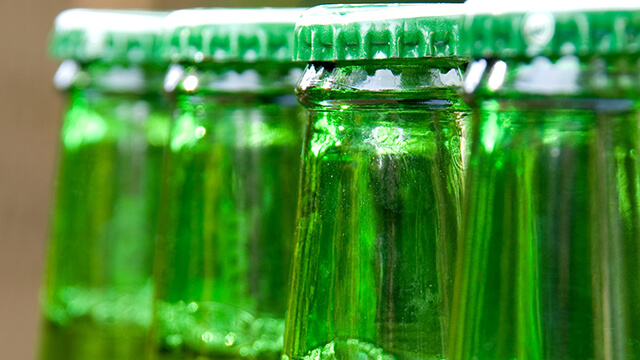
“There were lots of back and forth conversations, tweaks here and there in the plans, until we got to a point where we believed that we could redesign their current units and they could utilize what they had on site, rather than them having to buy-in new equipment.”
A key part of the redesign was increasing the number of plates in the units to increase the thermal surface area and so boost the efficiency of heat transfer.
Colin explains: “This is where it becomes a balance between cost and benefit in terms of adding more plates. We looked at the parameters the brewer was aspiring to achieve and what that balance looked like.
In the final redesign there are 518 plates in each exchanger, which is a lot, and the feedback we have had is that we found that balance perfectly and they are happy that the units are performing beyond expectations.
The brewery runs the two units back to back – so when one heat exchanger is taken offline for cleaning, the other steps into the breach. This boost in uptime gives the brewery operational continuity and certainty, and means those sustainability benefits are even greater as there is less cleaning in place and therefore significant savings in water, energy and chemical use.
Overall, in terms of the numbers, the original wort cooler was designed to recover 85% of the available energy but was actually operating at around 82%. After Alfa Laval’s changes and modifications, the units were boosted to operate at 88.1%.
On the glycol circuit, because the exchangers do not need to be run as hard or as quickly, the target of reducing energy was achieved, with a cut from 578kW to 373kW. Meanwhile energy can now be taken out of the hot wort – the pre-fermented solution – and put into water being used for the next brew, and the flow rate requirement for the next brew is reduced.
This is just the kind of circularity in performance that aligns with the brewer’s sustainability approach and an excellent example of Alfa Laval and its customers working together to deliver strong sustainable results.
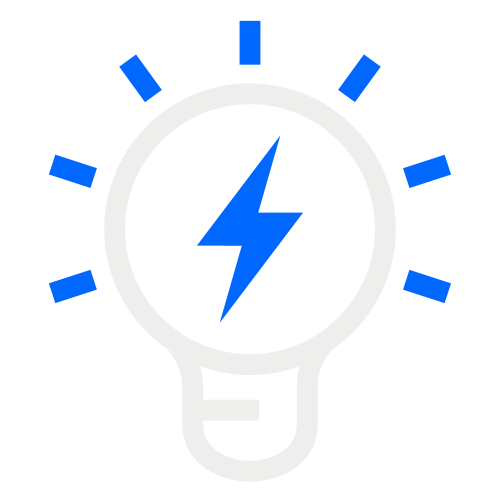
Energy savings: 1170 MWh/year

11200 m3 of water saved per year
Facts about the upgrade project
Alfa Laval has developed a range of premium heat exchangers perfectly designed for the brewing industry, where hygiene standards are of importance.
The special plate pattern ensures gentle treatment of the product and optimal flow distribution ensures superior cleanability and longer operating times.
Every detail – such as the leak chamber, interchangeable corners and five-point alignment – is carefully designed with service in mind and an extensive service offering is available to ensure top performance from the equipment throughout its life cycle.