UV or EC? Avoiding limitations in ballast water management
By understanding the limits of ballast water management systems, you can avoid limiting your vessel’s trade. All ballast water management systems have constraints, which are defined as System Design Limitations (SDL) in their type approval certificates. But some systems are more limited than others, and the limitations differ between UV solutions like Alfa Laval PureBallast 3 and electrochlorination (EC) systems. Know how you’ll be impacted.
- Keep temperature and salinity from becoming obstacles
- Handle even low-clarity waters with ease
- Avoid waiting – without increasing costs
- Access the ports that you need to reach
Trading efficiency for salt – salinity as an SDL
If you choose electrochlorination (EC), water salinity will be the most important System Design Limitation (SDL) for your ballast water management system. Electrochlorination is dependent on salt, so the type approval certificate will require a minimum water salinity in PSU. If you cannot provide it, you cannot comply.
If you call on ports with lower salinity, you’ll have to keep salt or salt water on board. High-salinity water is usually stored in the aft peak tank (APT), which can no longer be used for optimizing trim. If that’s the case, electrochlorination may increase your fuel costs by 2–5%.
If your vessel is a tanker, repurposing the APT could cost you even more. By reducing the available cargo capacity, it could keep it from winning contracts.
Want a deeper understanding?
To learn more about the issue of salinity, be sure to download our short guide to salinity, temperature and UVT.
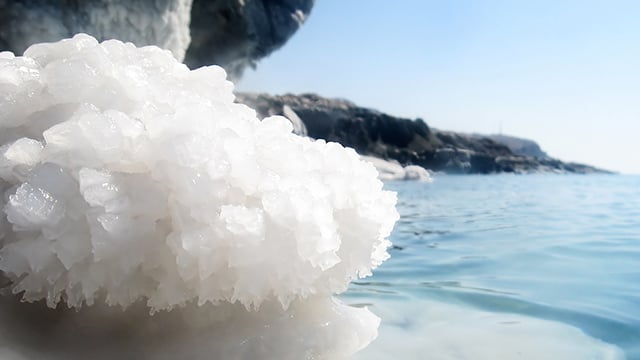
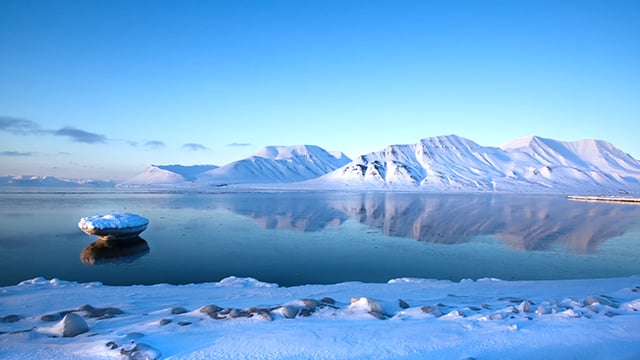
When cold means cost – temperature as an SDL
Electrochlorination (EC) is dependent on salt, but salinity isn’t the only System Design Limitation (SDL) that affects it. Its efficiency is impacted by the seawater temperature. If you choose an electrochlorination system for ballast water management, the type approval certificate will state a minimum water temperature for compliance – and most likely a higher recommended temperature.
Unless your vessel sails exclusively at warmer latitudes, you’ll need ballast water heating to stay compliant with electrochlorination. That will add CAPEX for heaters, as well as OPEX due to increased energy consumption. If you call on ports in very cold waters, electrochlorination may be a less feasible choice than UV treatment, which is completely unaffected by temperature.
Want a deeper understanding?
To learn more about the issue of temperature, be sure to download our short guide to salinity, temperature and UVT.
Keeping flexibility clear – UVT as an SDL
If you choose UV technology for ballast water management, water clarity is the most important System Design Limitation (SDL). However, its impact varies significantly between different UV systems. For the greatest possible freedom, you’ll want a system that handles waters with low UV transmittance (UVT).
Waters with low UVT are less clear and harder for UV light to penetrate. But an effective UV solution can still comply with ease. PureBallast 3, for example, handles UVT as low as 42% at full flow in IMO-regulated waters. By reducing power when the UVT is higher, a UV solution can save energy wherever the water is clearer – which is most ports worldwide.
Don’t be confused by UVI
When evaluating UV solutions, be wary of suppliers that promote UV intensity (UVI) rather than UVT. UVT is a standard measurement of water clarity, which makes it good for comparison. But UVI describes the amount of light hitting a sensor, which is relative to the distance from the lamp. For solution benchmarking, UVI has no meaning and is only used to mislead.
Want a deeper understanding?
To learn more about the issue of UVT, be sure to download our short guide to salinity, temperature and UVT.
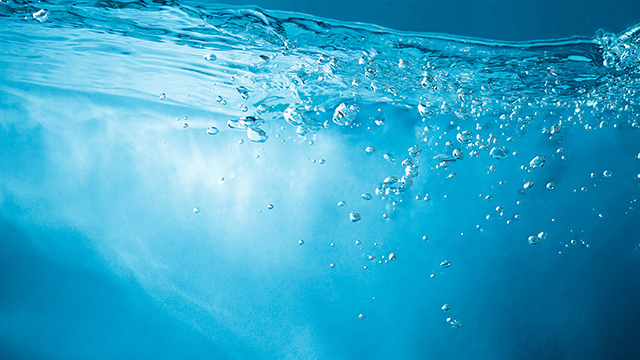
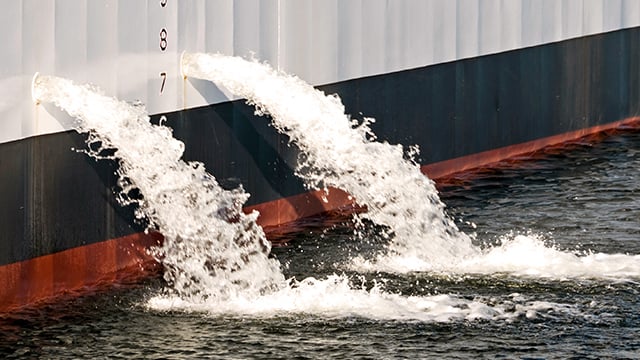
Make sense of holding time
Holding time (or hold time) is a required delay between ballast water treatment and ballast water discharge. It’s a System Design Limitation (SDL) that can apply to both UV solutions and electrochlorination (EC) systems, but how it applies differs between technologies.
EC holding time
Holding time for electrochlorination systems is misunderstood, because the type approval certificate tells only half the story. The SDL on the certificate is the holding time needed to neutralize the organisms, which may be zero if the hypochlorite dose is high enough. But there’s a backside to more hypochlorite.
Hypochlorite must be removed before ballast water discharge. This can be done by adding neutralization chemicals, or by waiting for the total residual oxidants (TRO) to decay. Shorter holding time during treatment means more neutralization chemicals and related cost – or else a longer post-treatment holding time, waiting for TRO to disappear.
UV holding time
For UV solutions, holding time is more clear-cut – and more varied. Some UV systems always have a holding time, while others almost never do. PureBallast 3, for example, has no holding time in IMO-regulated waters, which is around 95% of world ports.
Only in United States waters do all UV solutions have holding time. The reason is a difference in how IMO and the U.S. Coast Guard (USCG) define neutralization. (Our short guide explains.) Some UV solutions offer flexible ways to minimize USCG holding time, such as PureBallast 3, which can limit it to just 2.5 hours.
Want a deeper understanding?
To learn more about the issue of holding time, be sure to download our short guide to holding time.
Download our short guide
Time in the tanks always matters for EC
Even if an electrochlorination (EC) system has no holding time in its SDL, there’s every reason to consider how much time the water spends in the ballast tanks. During a longer journey, certain types of surviving organisms can reproduce, creating a non-compliance risk when the water is finally discharged. Whereas UV systems treat ballast water during both uptake and discharge, EC systems do only the first – so they have no means of removing this regrowth.
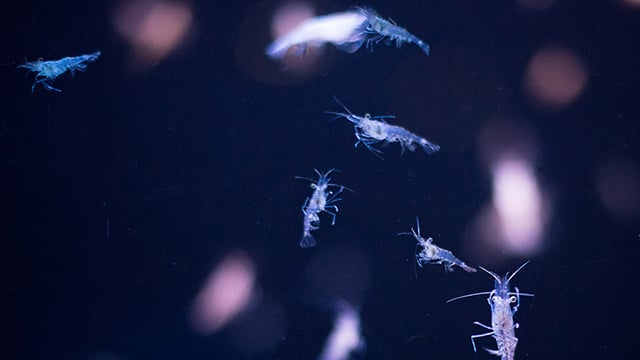
Make sure you have freedom to sail
Type approval isn’t the same as compliance – it’s only a qualifier. All ballast water treatment solutions have System Design Limitations (SDL), and staying compliant means staying within them. That affects where your vessel can sail, which why it’s important to compare type approval certificates. Compliance Navigator can help you start comparing. With this interactive tool, you can see the impact SDL will have along your trade routes, both for UV and for electrochlorination (EC).
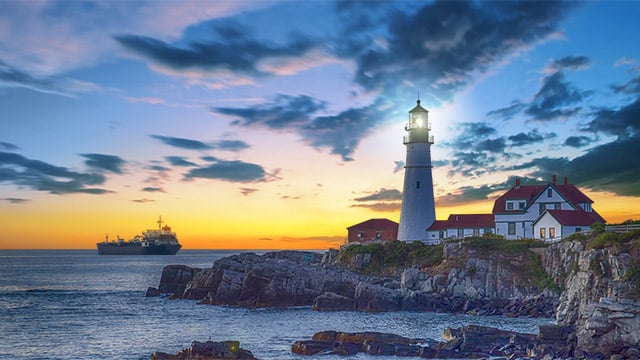
Shipowner insights into SDL
Millenia Maritime Inc. has chosen UV ballast water treatment with PureBallast 3 instead of electrochlorination (EC). System Design Limitations (SDL) were a major consideration, because Millenia wants operating flexibility for its MR tankers – including the option to sail efficiently in colder waters.
“It’s a matter of trading area, and these were key points that give Alfa Laval the highest performance,” says General Manager Francesco Ricciardi. “You can’t assume that your vessels will work in a specific area forever. Some of our vessels are ice-classed and can travel to Canada or Norway, for example. We have to be able to accommodate the charterer’s trade needs.”
Contact us to discuss the choice of UV or EC
Your choice of technology may be the most important one you make in ballast water treatment. We’d be happy to discuss it with you, in brief or in depth.