Aalborg Micro
The Alfa Laval Aalborg Micro is a uniquely compact water-tube economizer. Easy to install, operate and maintain, it reduces the use of the fired marine boiler by recovering heat energy that otherwise would be lost through the engine exhaust gas. Despite its minimal footprint, height and weight, the Aalborg Micro has an extended heating surface created by coiled fin tubes. Even more efficient than smoke-tube economizers, it provides an ideal retrofit solution where no other economizer will fit.
The most compact and efficient economizer available
- Extremely compact, plug-and-play design for easy retrofit
- Easy improvement of Carbon Intensity Indicator (CII)
- Short payback time (typically 1–2 years) through up to 25% fuel savings on the oil-fired boiler
- Reduced wear and maintenance on the fired boiler
- Internal damper for dynamic management of pressure drop
Reduce fuel costs and emissions
The Aalborg Micro is part of Alfa Laval’s broad waste heat recovery portfolio, which builds on over 40 years of waste heat recovery experience. We take a holistic approach, helping you identify the optimal economizer setup for your particular vessel.
Our solution is always tailored to your steam requirements, the amount of exhaust gas and your vessel’s unique characteristics. It can include:
- Smoke-tube or water-tube economizers
- Single-inlet or dual-inlet solutions
- Compact economizers to minimize installation footprint
You can always count on a rapid return on your waste heat recovery investment. Our broad portfolio, combined with our deep expertise, is your assurance of the most cost-effective, reliable and energy-efficient waste heat recovery solutions
Making room for energy efficiency
On three DFDS ferries, the Alfa Laval Aalborg Micro is recovering waste heat where it was once unthinkable. Five units of this compact and lightweight economizer fit where no other solution could, providing full coverage for the four main engines and genset on board. The result is significant fuel savings – and minimized emissions.
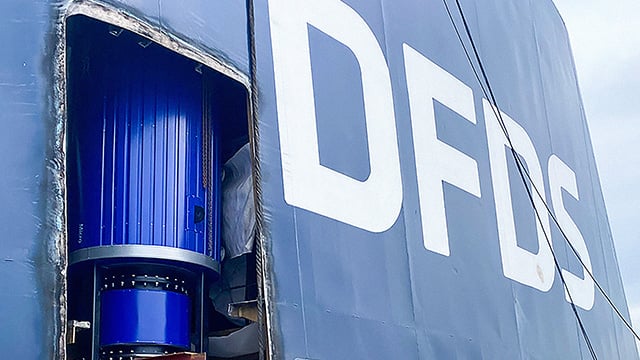
The Aalborg Micro is a game-changing solution with a tremendous potential in fuel savings - small and easy to install.
By reclaiming heat from auxiliary engine exhaust the Aalborg Micro gives a remarkable opportunity for saving fuel and maintenance cost. A typical retrofit installation saves enough fuel to reach payback in 1-2 years - and it is not only money being saved. CO2 emissions are reduced by around 900 tonnes annually.
Application
Only a portion of the fuel energy released by marine engines actually goes to propulsion. A large amount of it escapes as heat, and it makes sense to reclaim as much of this energy as possible. This is true not only for main engines, but for auxiliary engines as well.
Steam produced with the Aalborg Micro can support or fulfil steam needs in port, but it can also serve other functions. For vessels whose long-stroke main engines produce cooler exhaust, it can provide a needed steam boost during a voyage. Vessels that use blended fuels from 2020 onwards may also require additional steam, since these fuels will need to be stored at a higher ambient temperature – even if their pumping temperature is lower.
Working principle
The Aalborg Micro is installed after the vessel’s auxiliary engines (or small main engines). When the exhaust gas passes over the Aalborg Micro heating surface, the waste heat energy in the gas is absorbed for the production of hot water or steam.
The Aalborg Micro is not designed with its own steam space. It is used in connection with one or more oil-fired boilers, which act as the steam/water space. Forced circulation provides the Aalborg Micro with water at saturation temperature from the oil-fired boiler(s). The circulation pumps are located between the oil-fired boiler(s) – or a separate steam drum – and the Aalborg Micro.
In the Aalborg Micro, heat from the engine exhaust gas is transferred to the water side by convection. The generated steam/water mixture is then discharged into the steam space of the oil-fired boiler(s), where the heavier water particles separate from the steam.
Configuration examples
Steam plant optimization through waste heat recovery from auxiliary engines
Full redundancy for existing steam plant
How it works
Technical data
- Capacity: 500 kW up to 5 MW
- Weight (incl. insulation): 900–6600 kg
- Diameter (incl. insulation): 1070–1990 mm
- Height (incl. insulation): 1650–4280 mm
- Connections: Flanged
- Insulation: 100–200 mm
- Media inlet/outlet header: DN100
- Exhaust inlet/outlet header: DN450 to DN1000
- Maximum inlet temperature: 500°C
- Minimum outlet temperature: 130°C
- Pressure loss: <4500 Pa
- Maximum pressure:8 bar(g) (higher on request)