Features that set new standards
Improving the efficiency of the heat exchanger makes it possible to simultaneously maximize production while minimizing energy consumption. It’s about reducing both your power bill and your environmental footprint. That is why we have sought to boost thermal transfer with a revolutionary new plate design. The next-generation range of gasketed plate heat exchangers is filled with ground-breaking solutions that set new standards in thermal efficiency, mechanical reliability and ease of serviceability. These features are part of what sets Alfa Laval apart – you won’t find them anywhere else.
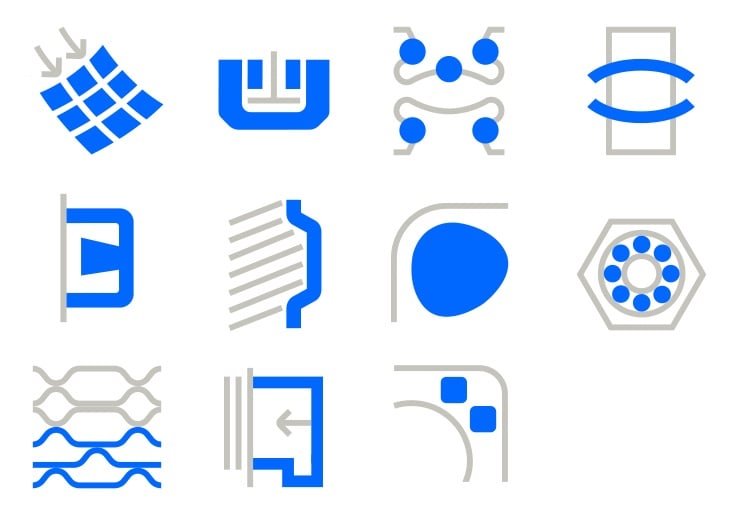
Features that improve heat transfer efficiency
Improving the efficiency of the heat exchanger makes it possible to simultaneously maximize production while minimizing energy consumption. It’s about reducing both your power bill and your environmental footprint.
That is why we have sought to boost thermal transfer with a revolutionary new plate design. A number of unique Alfa Laval features improve the flow of media across the plate and increase the overall heat transfer area. As a result, fewer plates are needed, meaning added performance and higher sustainability from an even more compact unit. Get more information and listen to our technical experts.
CurveFlow™
The CurveFlow™ distribution area optimizes the flow of media for better utilization of the whole plate surface. Improving the flow with more even distribution eliminates dead spots, providing higher thermal efficiency with reduced risk of fouling. This in turn means energy savings, lower maintenance costs and less time worrying about unplanned stops.
See how it works - CurveFlow™
OmegaPort™
The OmegaPort™ noncircular inlet and outlet offers two ways to save on energy: both higher thermal efficiency and reduced pump costs. That’s because it enhances the flow of media to give increased throughput, lower pressure drop and optimal utilization of the plate surface.
See how it works - OmegaPort™
FlexFlow™
The FlexFlow™ plate design improves thermal efficiency and optimizes pressure drop utilization. The asymmetric channels eliminate the compromise between thermal efficiency and pressure drop for duties with different hydraulic loads on the two sides of the heat exchanger. The result is up to 30% higher efficiency along with reduced fouling, for long-term, cost-effective performance.
See how it works - FlexFlow™
Offset gasket groove
The next generation of gasketed plate heat exchangers is designed with a gasket groove in a special zig-zag pattern that offers the greatest possible heat transfer area. Better utilization of the whole plate reduces the number of plates required for optimal performance and ensures maximum thermal efficiency for still greater energy savings.
See how it works - Offset gasket groove
Features that enhance robustness and increase reliability
Regardless of the industry or application, it goes without saying that you need a heat exchanger that is dependable. A broken or malfunctioning unit can waste time, hurt productivity and compromise safety – which ultimately cuts into your bottom line.
That is why we have aimed to increase the reliability of our gasketed plate heat exchangers in all aspects. We focus on durable designs based on robust materials and safe manufacturing processes. And in combination with advanced and innovative product features, you can be totally confident in your unit’s operation.Get more information and listen to our technical experts.
PowerArc™
The PowerArc™ plate pattern divider is a feature in the bigger plates of Alfa Laval’s next-generation heat exchangers. This design ensures a more rigid plate, preventing plate elongation and securing perfect alignment. As a result, the risk for leaks or damage to the plate is significantly reduced, meaning you can expect longer operation from every plate in the pack. Additionally, the increased rigidity makes handling plates during maintenance a safer and easier process.
See how it works - PowerArc™
Five-point alignment
Alfa Laval’s unique five-point alignment system ensures perfect plate alignment when closing the unit, while simultaneously making it quick and easy to remove plates during maintenance. Excellent plate positioning secures reliable mechanical performance and helps extend the life of your equipment.
See how it works
SteerLock™
The SteerLock™ plate alignment ensures reliable plate positioning and easy service. It also secures the plate pack when exposed to pressure and temperature during operation. If the unit is disassembled for maintenance, the smart design simplifies the picking of plates when they are about to be hung back.
See how it works - SteerLock™
RefTight™
The RefTight™ sealing system enables enhanced, long-term performance in applications with high pressures and temperatures. The weld is positioned outside the separate ring gasket groove, ensuring reliable sealing as well as extended gasket lifetime and prolonged service intervals.
See how it works - RefTight™
Features for simpler serviceability
The gasketed plate heat exchanger is built for many years of safe operation. One of the ideas behind a plate-and-frame design with gaskets is that it allows for a heat exchanger that is simple to open and close. This is important for inspection and service as well as for adapting the unit to new process conditions.
But as too many have discovered first-hand, sometimes opening and retightening the unit is anything but ‘simple’. With the next-generation gasketed plate heat exchangers, we have worked to make the opening and closing of a unit even easier.
And that’s just the start. New features make maintenance routines like regasketing and handling of the plates safer and easier than before. The combined result is service that goes faster – keeping the time the unit is out of production to a minimum. Get more information and listen to our technical experts.
ClipGrip™
ClipGrip™ gaskets offers superior fastening to the plate. Not only do the next-generation gaskets stay in place better than before, but they are also easier to mount in the first place. The unique design prevents snaking of plates at closing and the tangling of new gasket sets. Maintenance of the heat exchanger goes faster, plates and gaskets last longer, and you save money as a result.
See how it works
T-bar roller
In the next-generation plate heat exchanger, Alfa Laval has replaced the traditional roller function built on top of the carrying bar with a T-bar roller. The pressure plate roller is mounted under the carrying bar, decreasing the height of the heat exchanger and making maintenance simpler and more cost-effective. This design also protects the roller from falling dust and debris, which prevents jamming, minimizes the potential for damage to the frame and ensures easy opening and closing of the unit when required.
See how it works
Compact frame
The Compact frame feature offers more capacity in a smaller footprint. The smart guiding bar enables a maximum number of plates or cassettes in the frame while keeping the service area requirements down to a minimum. The design enables a faster and safer service which minimizes downtime and reduces maintenance costs.
See how it works
Bearing boxes
Alfa Laval’s large and medium model gasketed plate heat exchangers employ tightening bolts with bearing boxes to reduce friction when opening and retightening the unit. This makes it possible for one person to easily and safely service the heat exchanger without the need for special tools. The bearing box thus offers significant advantages over competing solutions designed with a simple nut and washer, where maintenance is laborious, time-consuming and potentially hazardous.
See how it works
Discover more watching our expert videos
Where would we be today without people who dare to challenge old ideas – the people willing to think outside the box? Setting new standards demands visionaries with know-how and a dedication to teamwork.
The advanced, new features of our heat exchangers are the work of talented experts at Alfa Laval. Let us introduce you to some of the team behind the next generation of gasketed plate heat exchangers.
Products applying the features
Carina introduces the next generation
Magnus introduces FlexFlow™
Mattias introduces SteerLock™
Kristina introduces Compact frame
Martin introduces CurveFlow™
Johan introduces ClipGrip™
Torgny introduces five-point alignment
Magnus introduces OmegaPort™
Jenny introduces the offset gasket groove
Sven introduces the T-bar roller
Göran introduces the bearing box
RefTight™ sealing system explained
Alfa Laval’s Materials Technology & Chemistry Lab and Test Centre
Our Materials Technology & Chemistry (MT&C) Lab and Test Centre are the homes to experts who possess industry-leading competence in materials science. From metals and polymers to in-depth chemical analyses, they offer unique services to help you resolve challenges and optimize your processes. And the knowledge they develop along the way is continuously reinvested to push our next-generation technology even further.
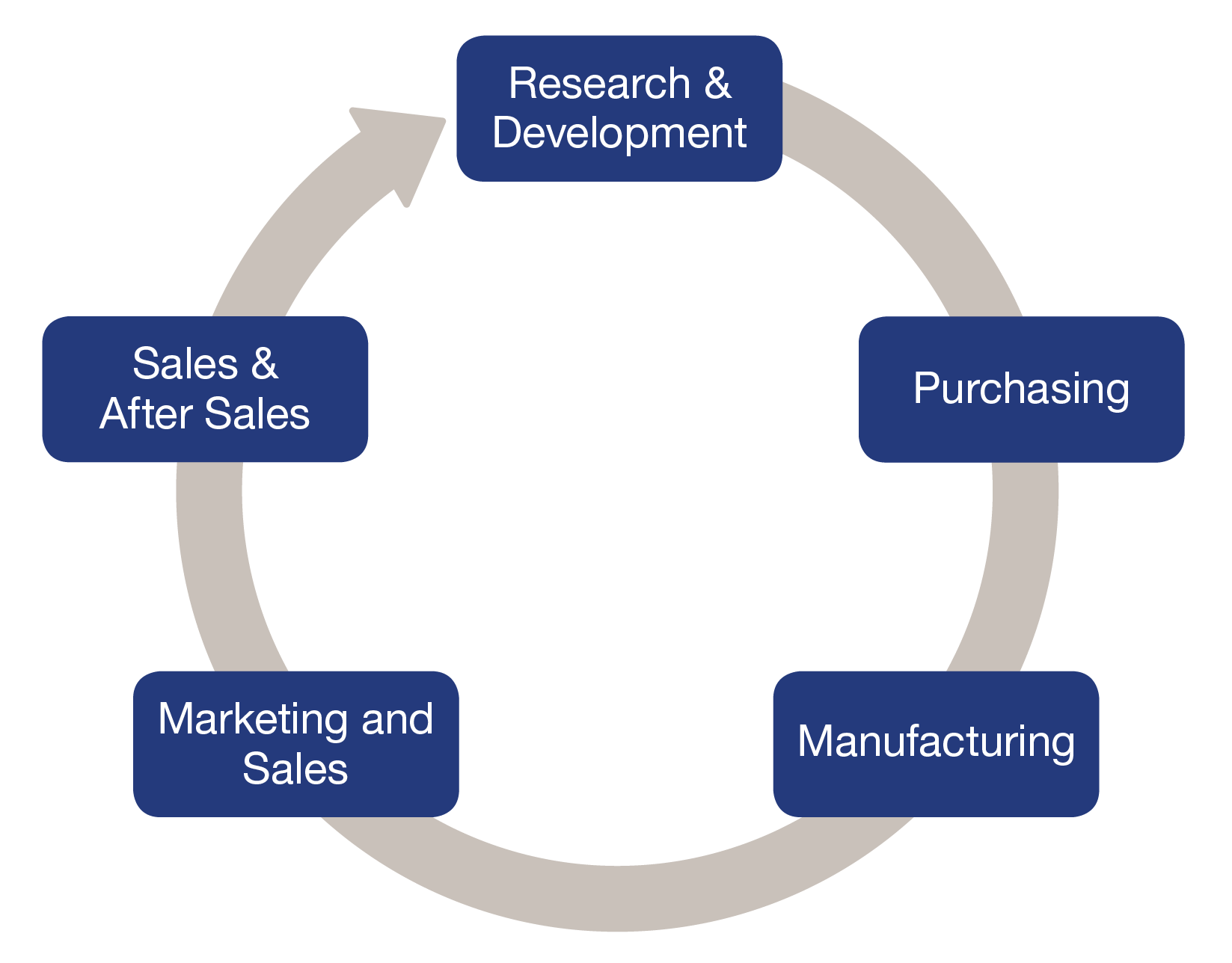
Alfa Laval Materials Technology & Chemistry Lab
Our materials specialists come from diverse backgrounds and are highly sought after in their fields. Get an introduction to Alfa Laval’s MT&C Lab and Test Centre, and learn more about how we work.
Metal fractography
The technicians in our lab can learn quite a bit by studying cracks in plate surfaces. Meet fractography expert Patrik, and learn more about how he uses this science to help customers resolve challenging operation issues.
Polymers and gaskets
With a large portfolio of gasket materials, we can always provide the ideal choice to match a customer’s processes. Hear from polymer expert Rasmus about our extensive testing procedures that ensure the most reliable gaskets.
Chemicals and fouling
There are many different types of fouling that can occur on a plate surface, and each can pose unique challenges. Chemistry expert Olga works closely with customers to resolve these issues and develop tailor-made cleaning protocols.
Unique expertise to ensure dependable sustainability over time
Chemistry experts in our materials lab really know about fouling – why it occurs, what it exists of, how and when to clean, what cleaning protocol to use and how to avoid risks already in the design phase. Listen to Olga that gives advice to our data center customers.
Contact us for more innovate technologies and patterns
New innovations and proven concepts together offer extensive benefits such as low total product life cycle cost, increased production output, minimized downtime and increased staff safety.
If you would like to have a talk with our experts about above features, please feel free to fill the form.